Trimming and punching are performed on trimming presses or friction presses. For particularly large die forgings (such as those produced on 10KN or 16K N hammers), hydraulic presses can be used for edge trimming.
Trimming dies and punching dies are mainly composed of punches (punches) and concave dies. When trimming, the forging is placed on the hole of the die. Under the push of the punch, the flash of the forging is sheared by the die and separated from the forging.
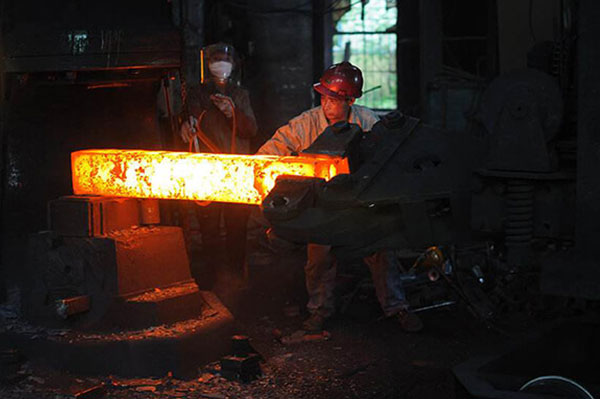
Because there is a gap between the punch and the die, bending and stretching occurs during the shearing process. Usually, the trimming punch pushes the forging and only plays the role of transmitting pressure, while the cutting edge of the die plays a shearing role. But sometimes the punch and die play a shearing role at the same time. When punching, the opposite is true. The punching die only plays the role of supporting the forging, and the punching punch plays the role of shearing.
Hot cutting and Hot Punching:
Use the residual heat of the forging immediately after die forging. Trimming and punching equipment and die forging equipment are organized in the same unit.
Advantages: The required trimming and punching force is small, and the forgings are not prone to defects such as cracks.
Disadvantages: poor working conditions and strict coordination requirements between trimming and punching and die forging processes.
Cold Cutting and Cold Punching:
After cooling, it is carried out uniformly, and the equipment does not need to be included in the die-forging unit.
Advantages: Good working conditions, high single-machine production efficiency.
Disadvantages: The required equipment is large in tonnage, and defects such as cracks are prone to occur in high-carbon and high-alloy steel.
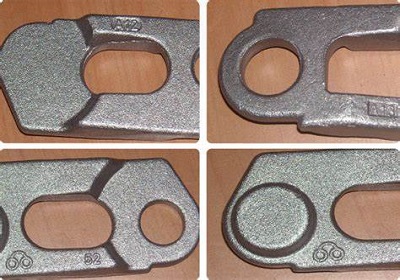
Principles for Choosing Cold and Hot Cuttings
Choose according to the material and size of the forging, the equipment conditions of the workshop, etc., and refer to the following principles.
- High alloy steel and high carbon steel forgings must be trimmed or punched in a hot state.
- Carbon steel or low alloy steel forgings with a carbon content of less than 0.45% and a weight of less than 0.5kg are generally trimmed and punched in the cold state.
- Large forgings are hot stamped to reduce the tonnage of required equipment.
- When heat correction and bending processes are required after trimming and punching, hot stamping should be used.
- When the forging is thick and the punch cross-section is small, hot punching should be used to prevent the punch from bending or breaking.
- For fork-shaped forgings, the burrs on the inner surface of the fork mouth are difficult to polish and the deformation is difficult to correct. If the tonnage of the equipment is sufficient, it is best to use cold-cutting edges.
Calculation of Trimming Force And Punching Force
- The force required for trimming and punching:

∂bA – Strength limit of forging material at trimming temperature (MPa);
A – shear area (mm²)
- When calculating the shear area of the flash and the skin, the calculation should be based on the actual thickness ht of the flash and the skin, as shown in the figure below:
Aact=L X ht
L – the circumference of the required trimming or punching area
According to the calculation result, select the edge-trimming equipment. Trimming presses are used in conjunction with die-forging equipment.