Press Line Automation
With many years of experience in the field of hydraulic press, Zhengxi provides dozens of press line automation for customers and is well accepted by all customers. In the press system, the real-time synchronous control system developed by Zhengxi, realizes synchronous control, real-time position monitoring, and following, and safe interlock between the robot and the press, robot and robot, thus maximizing the production efficiency.
It can effectively reduce the robot’s mechanical wearing, and improve the safety of the equipment and the OEE. Zhengxi combines with the actual needs of customers and integrates the decoiler, straighten machine, shear machine, washer, oiler, and other equipment. Provide customized and intelligent solutions, and keeps up with the international advanced level in technology and quality. Meanwhile, we have great advantages of low cost and local services. Our one-stop service for the whole line exempts our customers from future worries.
Video
Watch vidio below to learn more details.
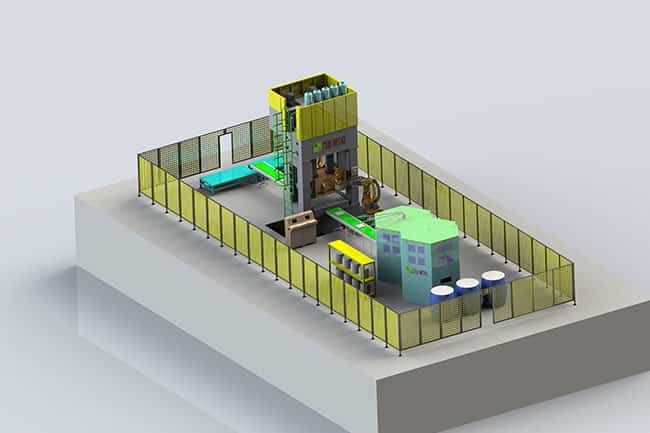
Extrusion Forging Automation
The hot stamping loading and unloading robot and production line are composed of a punching machine feeding manipulator, a punching machine unloading manipulator, a heating furnace feeding manipulator, a heating furnace unloading manipulator, a centering station, and a control system.
- The manipulator adopts double-speed and quadruple-speed telescopic manipulators with fast running speeds.
- The hot stamping robot completes a series of functions of steel plates from destacking to reclaiming, pres feeding, punching machine feeding, punching machine unloading, and other functions.
- In response to the requirements of the rapid operation of the manipulator with a large load and large stroke range, the Zhengxi robot has developed a box furnace-enhanced hot stamping forming production line.
- Each axis runs independently, with no multi-axis cumulative error, fast running speed, and long life.
- High repeat positioning accuracy and clamping positioning are more accurate than multi-joint robots.
- More cost-effective than the six-joint robots, and more suitable for large and small factories’ automatic matching processing.
- It can be easily matched with various detection sensors. (clamp head embedded, clamp head side-mounted sensor, side cover sensor, touch rod sensor)
Powder Mentallurgy Automation
It is mainly used for taking the powder before pressing. lt can be automatically and quickly metered and fed into the mold cavity, with a measurement accuracy of ≤1% (depending on the powder fluidity and thickness), and can achieve 7 beats/min.
The weight metering feeder adopts the weighing principle, which can also realize fully automatic control, and the metering accuracy of ≤0.1g can achieve 5 times/min beats.
Through the intelligent electronic scale to measure the weight and visually measure the size, it plays a detection role in the production line, and can quickly detect unqualified products and put them into the defective box.
The highest structure can be up to three down, and the accuracy can reach+0.005mm.
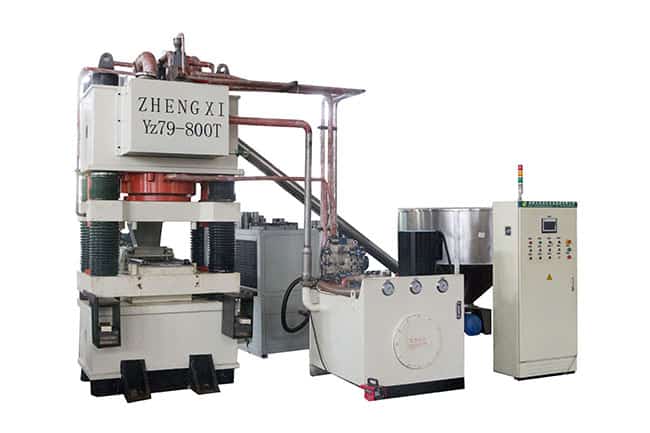
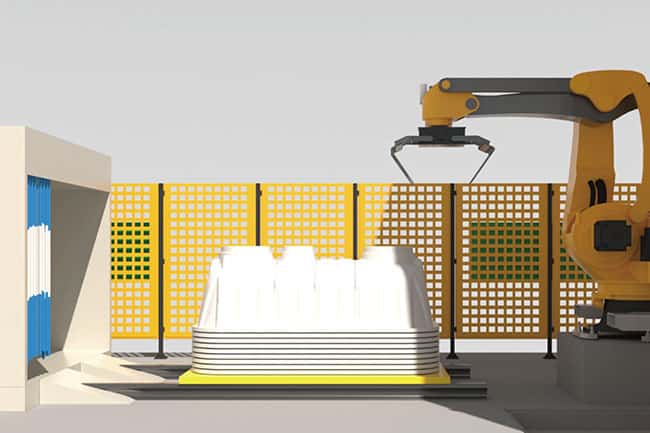
Heavy-duty Stamping Robot
Type: articulated robot, stepping manipulator, rapid heating insulation line, etc.
Netload: 0.1~3000Kg
Positioning accuracy: + 0.03mm
Shift beat: 1~12 pes/min
Temperature range: 0~1250C
SMC Sheet Automatic Feeder
- The equipment is mainly used to automatically feed the cut sheet into the press, and effectively lay the sheet on the mold, eliminating the need for manual paving in the press.
- The curing time in the mold can be shortened up to 1/3.
- Automatic paving, adaptable material paving, improving the safety performance of molding.
- One-time paving solves the problem of curing of the front material caused by slow manual paving.
- Installed in the front direction of the press feeder, it is connected to the equipment to realize automation. And the whole machine can be removed when not in use.
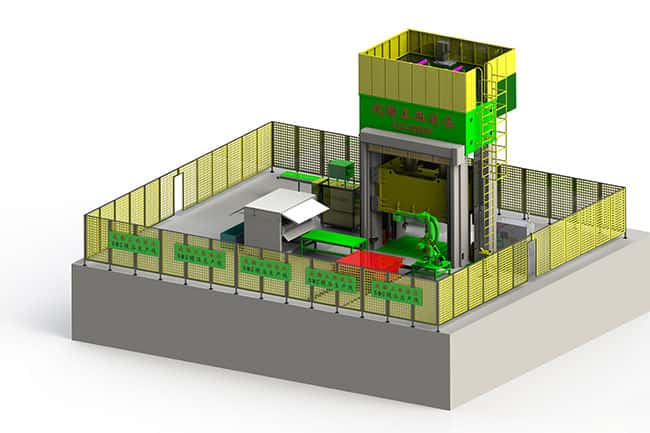
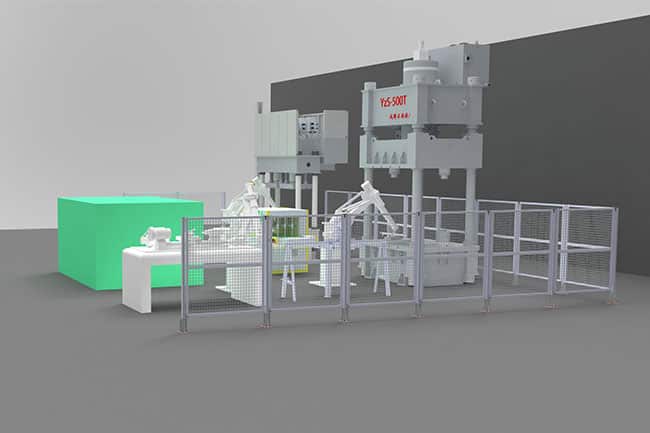
Composite Material Grabbing End Picker
- The customization scope of the end picker covers materials such as sheets, masses, prepress, gauze, woven materials, etc.
- Two types of end pickers, hot grab and cold grab at 20-300℃, can be customized for quick grabbing and quick release.
- Applicable workpiece: length 50-3000mm. width 50~2000mm, weight ≤50KGIt.
- It can be easily matched with various detection sensors (clamp head embedded, clamp head side-mounted sensor, side cover sensor, touch rod sensor)
- Multiple installation methods (axial, lateral, universal), convenient for debugging.
- The self-locking design can keep the clamped state even if the air is cut off.
Auto-industry Application
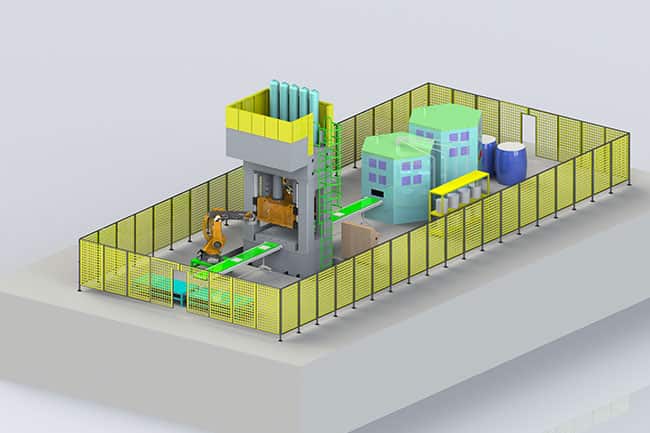
Composite material
- SMC sheet automatic feeder
- SMC sheet automatic tearing machine
- Measuring cutting machine
- BMC automatic metering and cutting machine
- Composite material grabbing end picker
- Automatic drilling and trimming machine
- Composite automatic forming production line
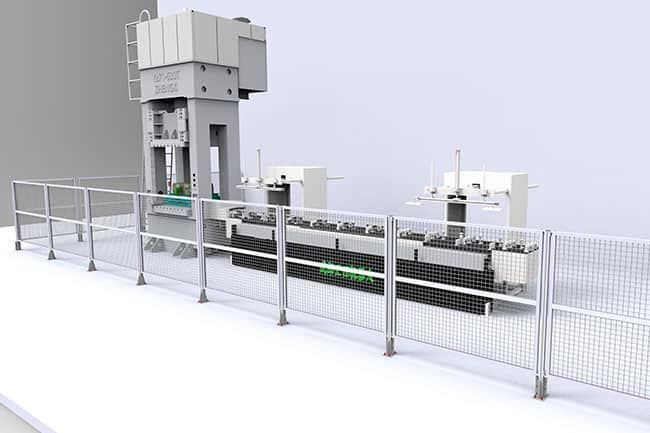
Sheet metal stamping
- Heavy-duty stamping robot
- Anti-theft door embossing production line
- Automatic stamping production line
- Automatic alignment platform
- Loading and unloading end picker
- Dcpalletizing and palletizing platform
- Stamping production line with machine
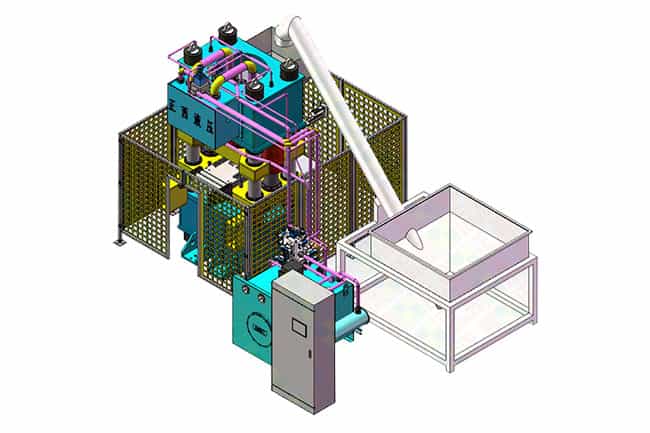
Powder metallurgy
- Metering feeder
- Size and weight test bench
- Automatic discharge swing tray palletizing platform
- Loading and unloading end picker
- High-precision special mold base
- Forming a high-precision control system
- Powder molding production line
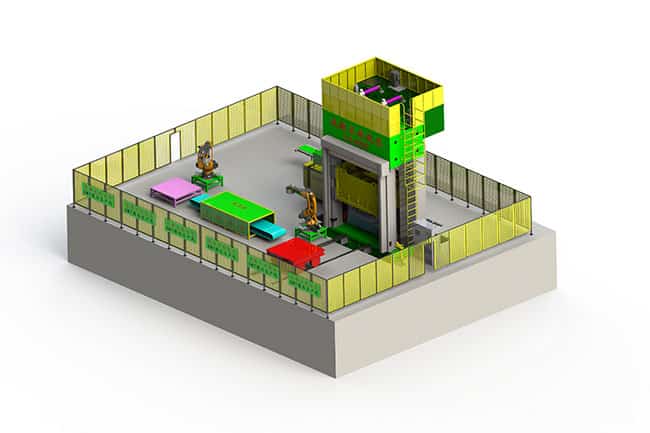
Extrusion forging
- Automatic temperature control system
- Loading and unloading end picker
- Automatic feeding device
- Automatic alignment platform
- Loading and unloading machine/manipulator
- Automated forging system
- Extrusion forging production line
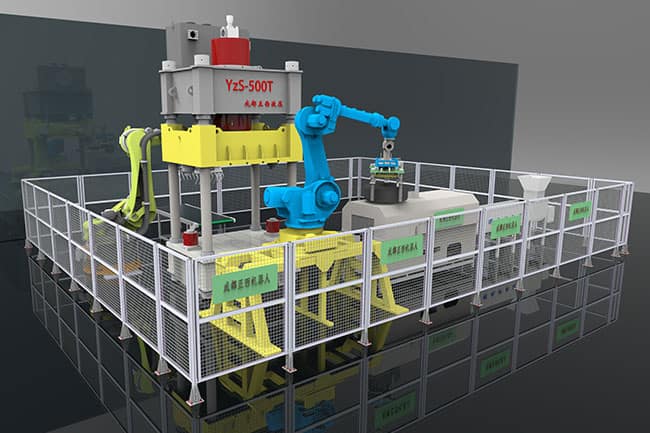
Equipping the internet of things
- Factory equipment IoT construction
- Equipment data collection record
- Information cloud platform construction
- Device loT motherboard development
- Product barcode labeling and storage
- Information exhibition App development
- Operation and maintenance system development and maintenance

Intelligent equipment
- Multi-axis linkage software and hardware development
- Multi-machine linkage software and hardware development
- Smart factory system customization
- Intelligent equipment R&D and manufacturing
- Production line AI system development
- Flexible MES system customization
- SCADA system customization