The forging trimming press is mainly used for the metal hot-cut edge-cutting process. Perform flash-cutting processing on the hot blank forged by die forging. Also known as die forging trimming press. According to the different forgings, the commonly used tonnages are 400 tons, 500 tons, 800 tons, 1000 tons, 2000 tons, etc. The machine structure is divided into two types: four-column type and frame type. It consists of a main frame, main working cylinder, return cylinder, ejection cylinder, hydraulic system, control system, safety protection device, and other parts.
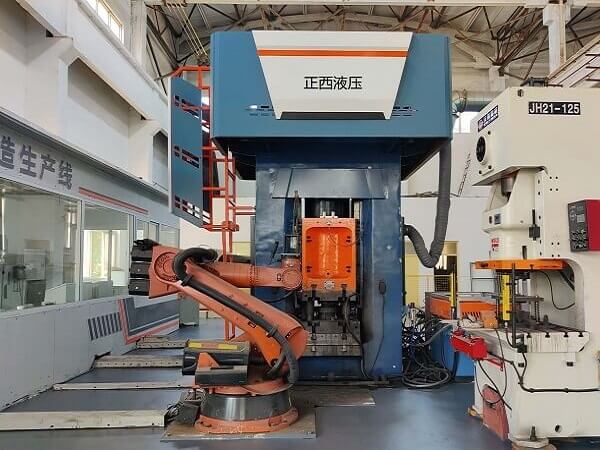
Features of Hydraulic Trimming Presses For Hot Forging
- The die-forging trimming press uses hydraulic transmission to generate power, squeeze the workpiece, and complete stamping, trimming, bending, stretching, and other tasks according to regulations.
- Centralized control using buttons. Process actions adopt relay control and other methods. Enables operating modes such as adjustments, manual and semi-automatic operations, and limited processing of workpieces.
- During the operation of the trimming press machine of forged parts, its working pressure, pressing speed, no-load rapid descent, and deceleration stroke range can be adjusted according to process needs, and it can complete constant pressure edge trimming and fixed stroke forming. These process methods have pressure maintaining, delay, and automatic return actions after pressing.
Structure of Forging Trimming Press For Sale
The main part of the trimming presses for hot forging includes hydraulic cylinders, beams, columns, and liquid filling devices. The power mechanism consists of high-pressure pumps, fuel tanks, electric motors, control systems, pressure valves, directional valves, and other components. The hot forging trimming press can be controlled manually or with a PLC control system. Energy conversion, regulation, and transmission are realized through pumps, oil cylinders, and various hydraulic valves to complete the cycle of various process actions. It has an independent power mechanism and electrical system.
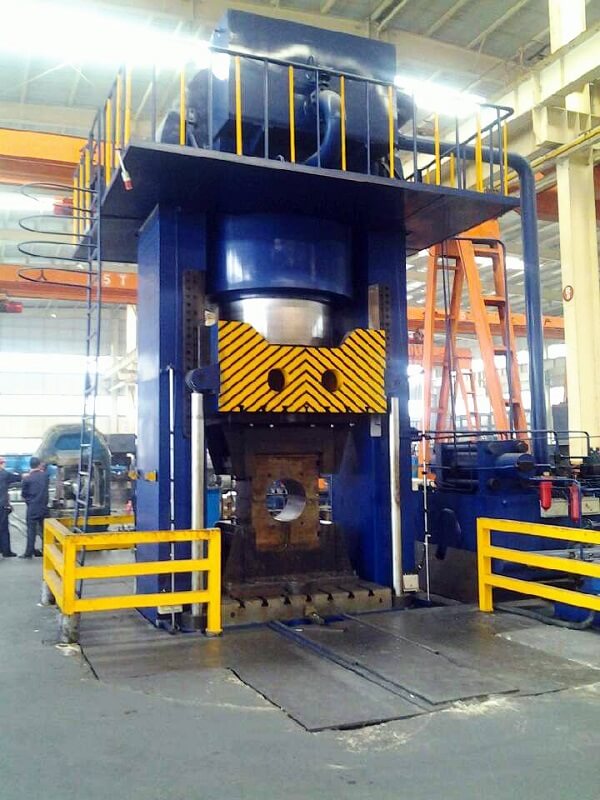
Workflow of Trimming Press of Forged Parts
Most trimming presses of hot forgings adopt the form of three-beam and four-column push-ups. The hydraulic cylinder piston is of plunger type. Three large-diameter master cylinders are installed on the upper beam to output forging or trimming pressure. Two small-diameter lifting cylinders are installed on both sides of the upper beam for return stroke and pressure re-gathering. During rapid edge trimming, the main hydraulic pump starts. The hydraulic system circuit builds up the overall pressure guides the electromagnetic reversing valve to obtain current, and pushes the pressure oil into the three main hydraulic cylinders.
Then the other solenoid directional valve gets current. The cartridge valve is activated, driving the two lifting cylinders to communicate with the main cylinder, prompting the movable beam to move downward, which forms differential trimming or forging. When the edge trimming is completed, the electromagnetic reversing valve is powered on, and the three main hydraulic cylinders pass through multiple cartridge valves respectively, forming a three-stage rapid unloading state.
When the pressure in the system drops to the preset pressure, the electromagnetic reversing valve is powered on. The pressure oil is prompted to enter the recovery cylinder, and the filling valves on the three main hydraulic cylinders are opened. The edge-cutting hydraulic press relies on the recovery of the remaining pressure energy in the cylinder and the oil supply from the main hydraulic pump to make the movable beam move upward quickly, which completes an edge-cutting cycle.
Then through pressure or stroke control, the die forging hot edge press automatically enters the next cycle, forming a fast forging and fast cutting cycle.
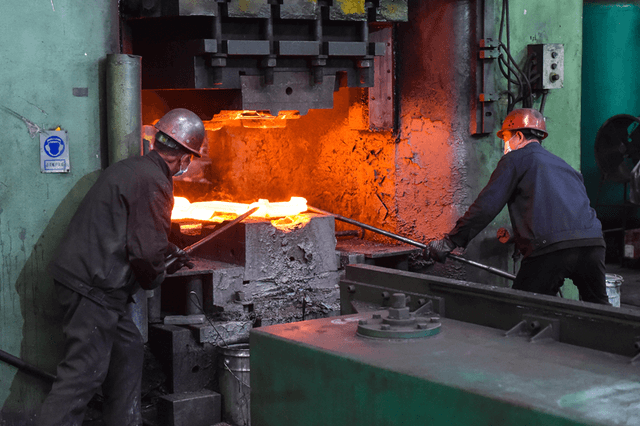
Performance Advantages of Hydraulic Trimming Presses For Hot Forging
To utilize waste heat, the hot forging trimming press must cooperate with the die forging equipment according to a certain production rhythm. Trimming productivity is limited by the productivity of the die-forging machine. The pressure required for hot cutting is much smaller than that of cold cutting, the material has good plasticity, and the incision is not prone to cracks, but it is prone to deformation.