1250T Deep Drawing Press Machine With Moving Bolster
1250T Deep Drawing Press With Moving Bolster
This series of hydraulic presses are double-action sheet drawing hydraulic presses, especially suitable for the drawing, flanging, bending, and stamping processes of metal sheet parts. It can also be used for general pressing processes. The stamping processing method uses a mold to form a flat blank into an open hollow part during the stretch-forming process.
Working Conditions
1)Ambient temperature: -5℃~45℃。
2)Relative humidity: ≤85%, No condensation.
3)Running Ability: Support 24-hour continuous production
4)Power supply: 320-520V, 60/50HZ TN-S
5)Air Supply: Dg15mm, 0.4~0.6Mpa.
6)Water Supply: Water Pressure 0.2~0.3Mpa, Cooling Water≤30℃, CL of cooling water<25ppm.
Total Power: Around 200HP.
Video
Watch the video below to learn more details.
Main Body
The design of the whole machine adopts computer optimization design and analyzes with finite elements. The strength and rigidity of the equipment are good, and the appearance is good. All welded parts of the machine body are welded by high-quality steel mill Q345B steel plate, which is welded with carbon dioxide to ensure the welding quality.
The upper beam, lower beam, slider, and side beams are welded by steel plates. Confirm that the welds are free of bubbles and welding cracks. Anneal after welding to eliminate welding stress.
The sliding block is guided by four corner and octagonal guide rails, and the column rods are 45# forgings, which have been normalized. The contact surface between the guide rail and the sliding block is made of copper material, which has good wear resistance, long service life, and high adjustment accuracy, and the sliding block runs smoothly without jitter.
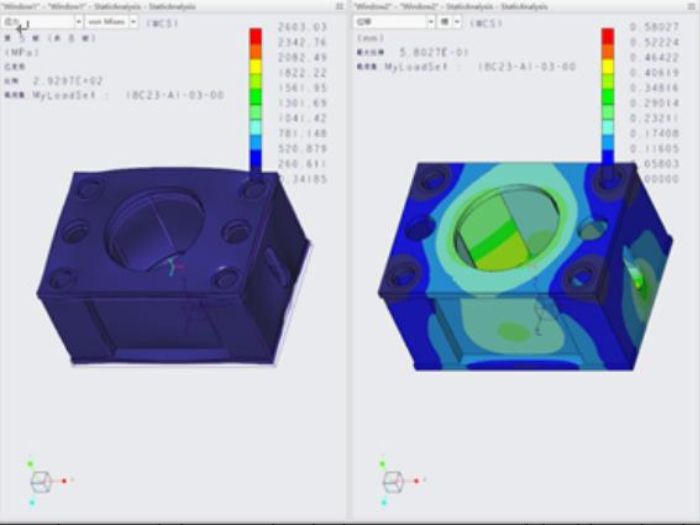
Main Body Parts
Parts | Feature |
Cylinder Barrel | 1. Made by 45# forged steel, quenching and tempering 2. Fine grinding after rolling |
Piston Rod | 1. Made by Chilled cast iron, quenching and tempering 2. The surface is rolled and then chrome-plated to ensure surface hardness above HRC48~55 3. Roughness 0.8 |
Seals | Adopt Japanese NOK brand quality sealing ring |
Piston | Guided by copper plating, good wear resistance, ensuring long-term operation of the cylinder |
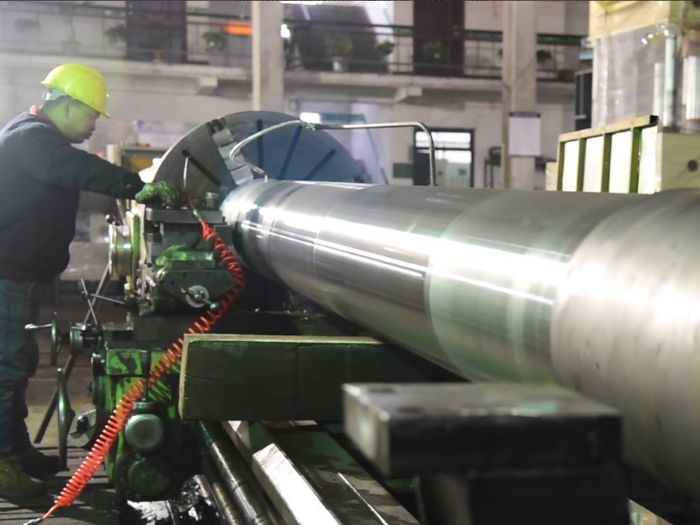
Pillar
The guide columns (pillars) will be made of C45 hot-forging steel. The guide sleeve adopts a copper guide sleeve, and the slide guiding system is an 8-point gib guiding system with replaceable phosphorus bronze linear.
Servo System
Compared with the traditional variable pump system, the servo oil pump system combines the fast step-less speed regulation characteristics of the servo motor and the self-regulating oil pressure characteristics of the hydraulic oil pump, which brings huge energy saving potential, and the energy saving rate can reach up to 30%-80%.
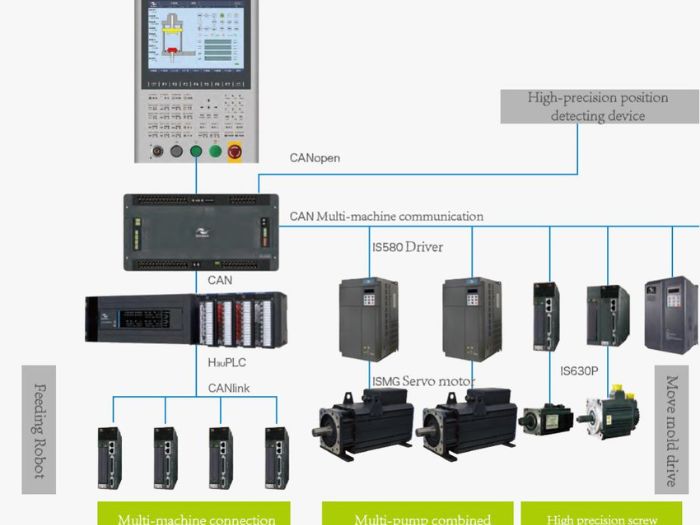
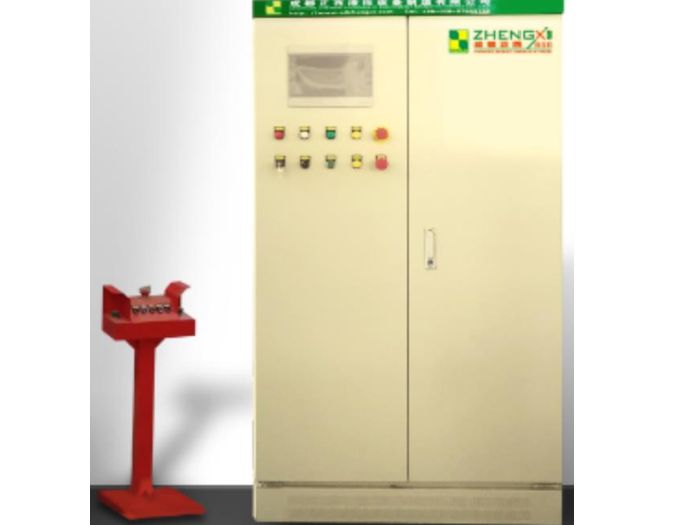
Electrical control system
The electrical system consists of a power circuit and a control circuit. The power circuit is AC320-500V,50-60HZ, TN-S, which is responsible for starting, stopping, and protecting the oil pump motor. The control circuit system adopts a PLC programmable controller combined with a touch screen main control to realize various process action cycles of the machine tool.
Hydraulic System
The upper fuel tank is arranged on the rear side of the upper cross beam and is used to control the movement of the slider. Arrange a fuel tank cleaning window cover on the side of the fuel tank. The oil pump motor unit and the hydraulic control valve block are arranged in an orderly manner on the upper surface of the fuel tank. The hydraulic pipelines and cable routing pipes (grooves) are arranged neatly and standardized.
The hydraulic oil pipes are mainly cold-drawn pipes, the joints are ferrule joints, and the large-diameter oil circuits are connected by flanges. The pipeline connection is as far as possible to use flange connection and butt welding, welding effect is good, effectively solving the problem of oil leakage caused by poor welding.
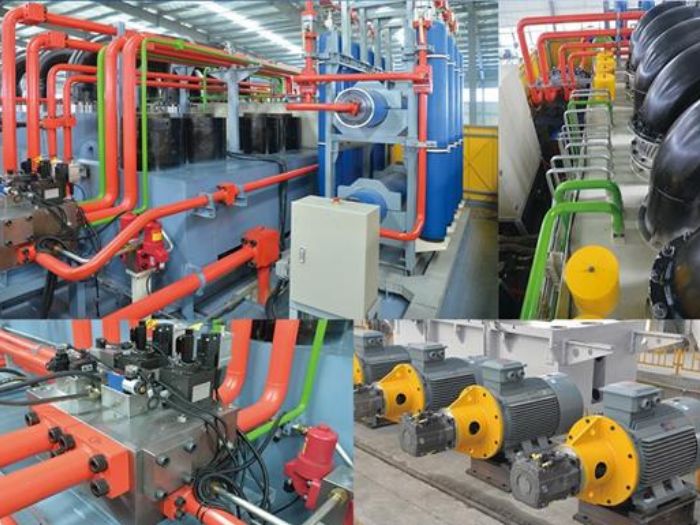
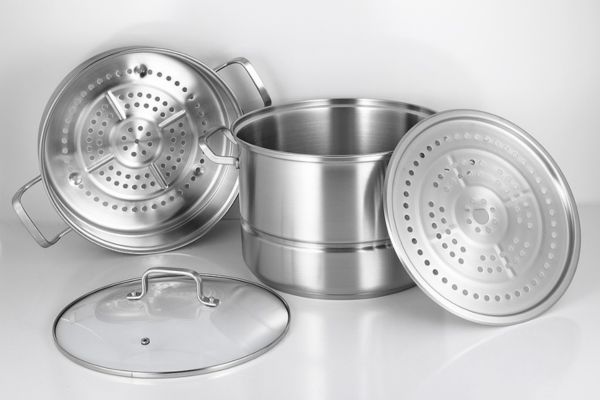
Applications of Deep Drawing Press
The deep drawing press machine is mainly suitable for sheet metal part processes such as deep drawing, crimping, forming, blanking, punching, correction, etc., and is mainly used for quick stretching and forming of sheet metal.
The stamping drawing press machine is been designed as an assembled H-frame which has the best system rigidity, high precision, long lifetime, and high reliability, and is used for pressing sheet metal parts and can meet the demand of production at 3 shifts/day.
Deep Drawing Press Parameter
Name | Unit | Value | |
Name of machine |
| Deep drawing Hydraulic Press | |
Model |
| Yz27-1250T | |
Main cylinder pressure | KN | 12500 | |
Return Capacity | KN | 1000 | |
Max. liquid pressure | MPa | 25 | |
Daylight | mm | 2200 | |
Main cylinder Stroke | mm | 1800 | |
Die close height | mm | 400 | |
Die Cushion stroke | mm | 500 | |
Die Cushion force | KN | 4000 | |
Worktable size
| LR | mm | 3500 |
FB | mm | 2200 | |
Die cushion size | LR | mm | 2320 |
FB | mm | 1420 | |
Slider speed | Down | mm/s | 450 |
Return | mm/s | 400 | |
Working | mm/s | 5-30 | |
Die cushion speed | Ejection | mm/s | 55 |
Return | mm/s | 80 | |
Moving bolster stroke | mm | 2200 | |
Moving bolster size
| mm | 3500*2200*860
| |
Moving bolster speed | mm/s | 50~80 | |
Punching Damper Force | KN | 2000 | |
Motor Power | KW | 90 |