Fender refers to a covering part on motor vehicles and non-motor vehicles. It is located outside the body of the wheel. It is a plastic material with a certain elasticity. The front and rear fenders can be divided according to the installation position. Its structure includes front fenders, front fender linings, front fender lights, and rear fender light radiator frames. There are two production processes for fenders according to their molding materials. One is stainless steel plate stamping, and the other is SMC composite material compression molding. Here, we introduce a 1200-ton four-column hydraulic press, which is hydraulic press equipment for SMC car fender molding.
Our SMC car fender molding hydraulic press is a composite press with a three-beam, four-column, and double-cylinder structure. It is mainly used for the hot-pressing molding of fiberglass and composite materials. It produces various automotive accessories, such as engine hoods, bumper covers, automobile fenders and other parts. In addition, a heating mold and its corresponding temperature control system can be installed to hot-press the raw materials in one step.
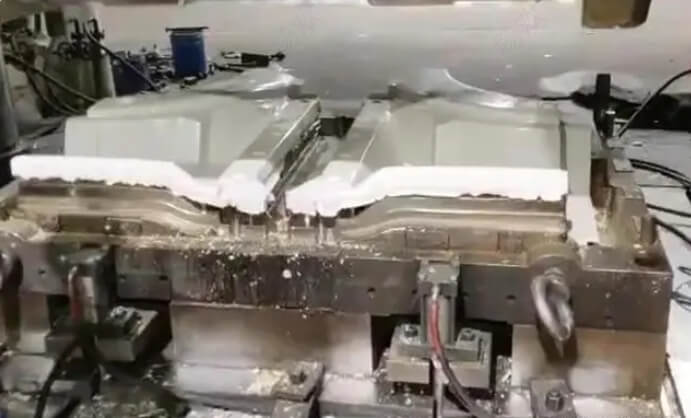
SMC Fender Molding Process Steps:
- Preheating the mold. The mold includes an upper mold and a lower mold.
- Unloading. Cut the material to be processed into a pre-designed shape.
- Stacking. Stack the material on the mold of the 1200-ton SMC automobile fender molding hydraulic press.
- Mold closing and curing. The 1200T composite hydraulic press closes the mold at a preset speed and performs pressure holding and curing. During the molding process, the hydraulic press can achieve fast descending, pre-pressing, deflation, working, pressure holding, cylinder pressure, slow mold opening, fast return, slow demolding, fast ejection, ejection stop, fast return and other actions. It can also increase the functions of deflation segmentation (up to 6 segments), pressure compensation and stabilization, temperature multi-point control, and fast pressurization.
- In-mold spraying. Open the upper mold and the lower mold to the predetermined position. Inject the conductive primer at a predetermined pressure to expand the conductive primer to cover the fender’s surface, then pressurize and cure.
- Cooling and shaping. Place the demoulded fender on a tooling to cool and shape it.
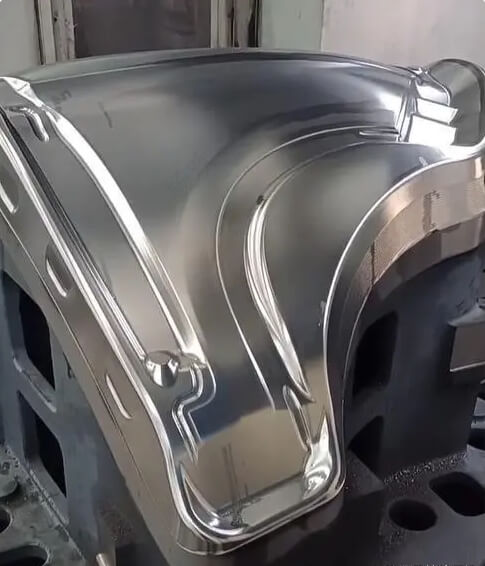
Features of 1200-ton SMC Car Fender Molding Hydraulic Press:
- Hydraulic control adopts an integrated cartridge valve system. Reliable action, long service life, small hydraulic shock, reduced connection pipelines and leakage points.
- The 1200-ton four-column hydraulic press is designed through an optimized three-beam four-column structure, which is simple, economical and practical.
- Independent electrical control system, reliable operation, intuitive action, and easy maintenance.
- It has three operation modes: adjustment, manual and semi-automatic.
- Through the operation panel selection, two operation processes of fixed stroke and fixed pressure can be realized, and it has functions such as pressure holding and delay.
- The working pressure of the slider of the SMC automobile fender molding hydraulic press, the formation range of no-load fast downward and slow working advance can be adjusted according to work needs.
- Low noise configuration: Due to the use of a low-noise motor pump group and noise reduction measures, the noise of the composite material press produced is lower than conventional.
- Storage configuration: When the press maintains pressure to take materials, lay materials, and take parts, the oil pump energy is stored and released during operation. In this way, the total power of the motor can be reduced.
- The servo motor is used, the working noise is low, the press runs smoothly, and the control is more precise.
- The forged steel is finely processed and thickened, with good rigidity and strong resistance to deformation.
- Well-known brand control systems and electrical components are used.
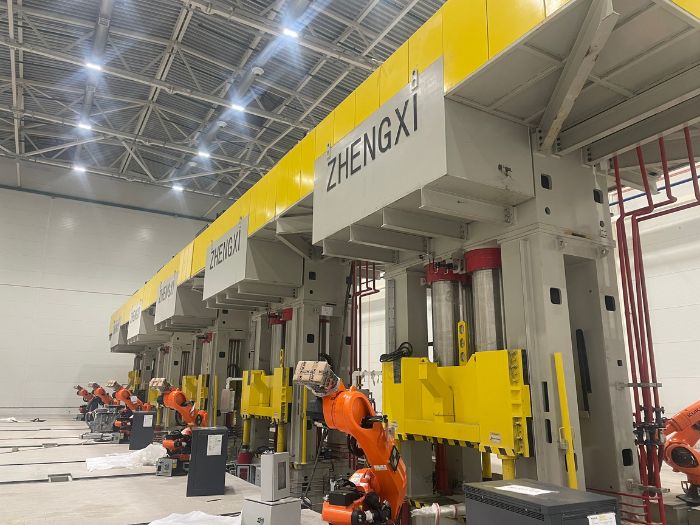
SMC car fender molding hydraulic press has a variety of structures, including four-column type and frame type. The main machine of this 1200-ton four-column composite molding press introduced in the article comprises an upper crossbeam, a slider, a workbench, a column, a main oil cylinder and an ejection cylinder (optional). Four columns serve as the main frame, and the upper crossbeam and the workbench are fastened to the two ends of the four columns by locking nuts to form a closed body. The main oil cylinder is installed in the hole of the upper crossbeam, and the slider is connected to the main cylinder piston rod flange, relying on the four columns to guide up and down movement. The slider is equipped with a guide sleeve, and the slider and the workbench surface have “T” grooves for fastening and installing the mold.
The hydraulic system device is arranged on the right side of the fuselage. The hydraulic control system mainly consists of an oil tank, an oil pump motor group and a two-way cartridge valve. It is a mechanism that generates and distributes working oil to enable the main machine of the molding hydraulic press to achieve various actions. The oil tank is a steel plate welded part, and the motor oil pump and the two-way cartridge valve group are placed on the upper part of the oil tank. The system is centralized and compact, making it easy to inspect, adjust and maintain.
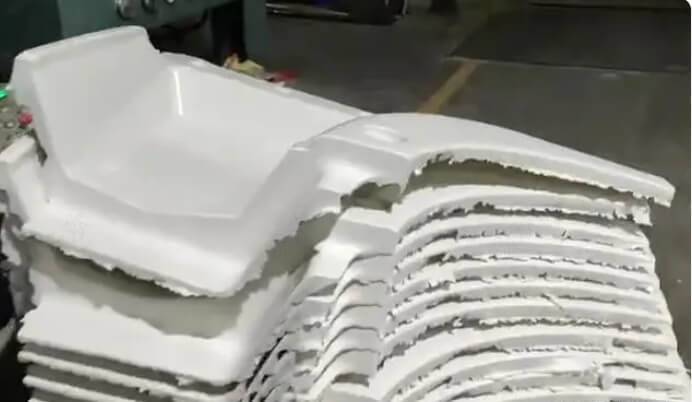
The hydraulic system adopts an integrated cartridge valve system, which has the characteristics of sensitive action, reliable operation, and good sealing performance. The hydraulic system is reliably sealed and leak-proof. Flanges connect the main pipelines, and the pipelines are equipped with anti-vibration measures. The two-way cartridge valve group is a new type of hydraulic component, which has the characteristics of small flow resistance, large oil flow capacity, fast action speed, good sealing performance, no leakage, not easy to get stuck, strong anti-pollution ability, small size, long life, easy maintenance, etc.
Chengdu Zhengxi Hydraulic Equipment Manufacturing Co., Ltd. is a well-known hydraulic press manufacturer in China that provides high-quality automotive leaf blade forming presses. If you need anything, please contact us.