1. Shape and Use of the Head
The head is the end cap on the pressure vessel and is a major pressure-bearing part of the pressure vessel. The shapes are spherical, oval, dish, spherical crown, cone shell, flat cover, etc. The head is an indispensable and important part of the pressure vessel equipment in many industries from petrochemical, and atomic energy to food and pharmaceutical. And it is related to the long-term safe and reliable operation of the pressure vessel. The material of the head is mostly carbon steel, stainless steel, alloy steel, etc.
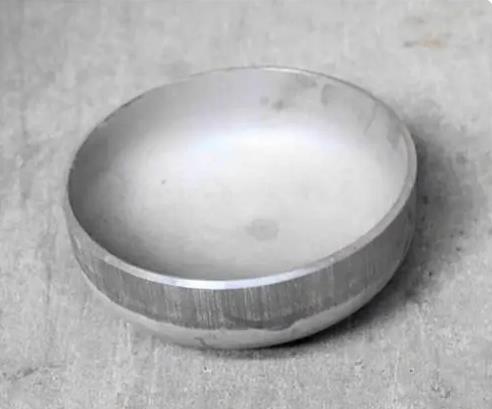
2. Head Processing Method
(1) Stamping. To adapt to mass production, and to press thick-walled and small-diameter heads, multiple sets of head molds are required.
(2) Spinning. Some ultra-large and ultra-thin heads, especially in the chemical industry, are mostly large and small batches, which are especially suitable for spinning. The oval head is very suitable for spinning, while the dish head is rarely used, and the spherical head is more difficult to press.
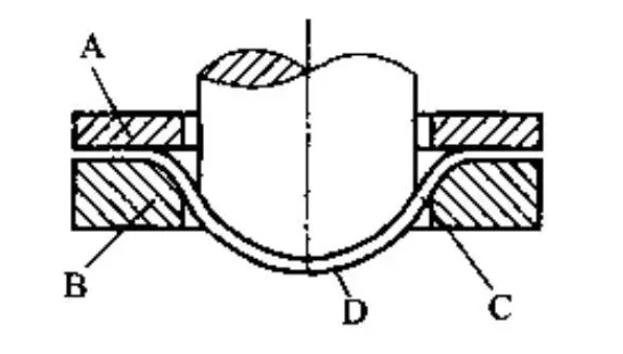
3. Head Processing Equipment and Tools
(1) Heating equipment. Large factories mostly use gas furnaces. The current heating adopts chamber type or reflection type heating furnace. Use oil or gas heating whenever possible. Because it is characterized by clean combustion, high efficiency, easy temperature control, unfavorable overburning, and difficult decarburization. The heating furnace should be equipped with a temperature measuring device and a temperature recorder.
(2) There are two types of head-forming hydraulic presses: single-action and double-action. There are also two types of water pump presses and oil presses. Single action means only stamping cylinder, no edge cylinder, only small and medium factories are using it. Large factories all use double action, that is, there is a blank holder cylinder and a stamping cylinder. The transmission medium of the water pump press is water, which is cheap, moves quickly, and is not stable. The sealing requirements are not as high as that of the hydraulic press, the efficiency is lower than that of the hydraulic press, and the guiding requirements are not strict.
The transmission medium of the hydraulic press is oil, and changing the oil is more expensive than water. Stable transmission, high requirements for sealing, high requirements for guidance, high requirements for oil, poor oil filtration, or quick reversing. Closing the oil circuit will cause an impact on certain actions in the system, making the movement of the press unstable, so it is necessary to filter the oil frequently, change the oil on time, and thoroughly clean the oil circuit and fuel tank when changing the oil.
(3) Use tooling. Forming upper and lower molds and feet of various heads (must be checked and accepted according to relevant technical conditions. There should be no pores, shrinkage, slag inclusions, etc. The accuracy of geometric dimensions and curves can only be used after passing the inspection).
(4) Common tools. Fastening wrench, sledgehammer, crowbar, steel ruler, tape measure, photoelectric thermometer, internal and external calipers, handling tools, etc.

4. Compression of the head
When pressing, the head blank should be placed as concentrically as possible with the mold. The offset between the blank and the center of the lower die should be less than 5 mm. When pressing the perforated head, it should be noted that the elliptical opening of the blank is placed in the same direction as the long and short axes of the mold. During the pressing process, the manhole punch is first aligned with the opening position of the blank and ejected. Push it to a place slightly higher than the plane of the lower die (about 20 mm), then the upper die presses down again, and the manhole punch also falls down at the same time to press the head into shape. When pressing, the punching force should be increased slowly from small to small, and should not increase or decrease suddenly.
When the hot stamping head is cooled below 600 degrees, it can be dragged away from the mold for lifting, and must not be placed in the tuyere. Do not stack more than two pieces until they have cooled to room temperature. During continuous stamping, the die temperature rises to about 250°C, and stamping should not be continued. After cooling measures are taken to lower the temperature of the die, the work can continue. The perforated head should be formed once as much as possible. When it is not possible to form it at one time due to conditional constraints, attention should be paid to the concentricity with the head when punching the manhole, and attention should be paid to keeping the wall thickness at the flange of the manhole uniform.

5. Process Flow of Cold-pressed Head
The initial position of the head forming hydraulic press → the stretching slider and the blank holder slide down quickly together → the blank holder slides down quickly separately → the blank holder slider pressurizes → the stretch slider goes down and stretches the workpiece → holding pressure delay and pressure relief → Stretching slider Return of blank holder slider → Jack up the rotary device to jack up the workpiece → (after the workpiece is removed) Jack up the rotary device to return. The start time of jacking up the rotary device can be activated by the position set in the return stroke of the slider to increase the working frequency.
Zhengxi is a famous hydraulic press supplier in China that provides high-quality metal tank head-forming machines. Using it to manufacture metal heads is very easy. Contact us to know more!
