The manufacturing of a car starts with the chassis. In the past, chassis were constructed from very heavy welded steel components. This results in reduced fuel economy. With the emergence of advanced hydroforming manufacturing processes, the components of today’s automotive chassis have become lighter and stronger. At the same time, fuel economy is also improved to a certain extent. Below we will introduce how the automobile production line uses hydroforming technology to produce automobile chassis parts.
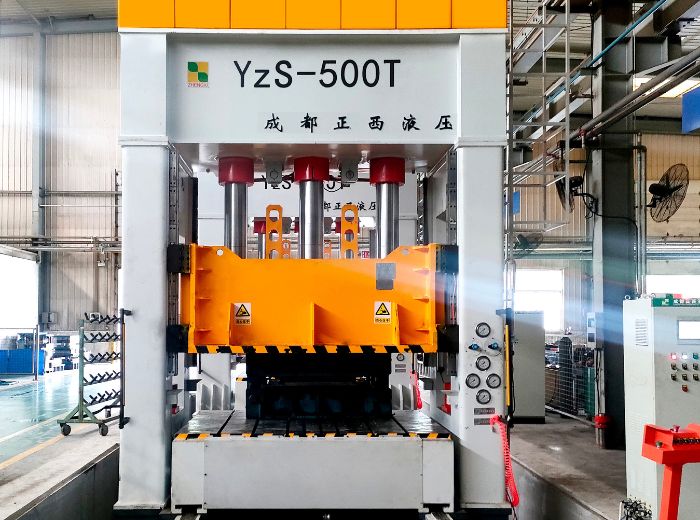
Step 1
Put the steel pipe into the CNC three-dimensional pipe bending machine. Use with the mandrel to prevent wrinkles or folds in the pipe wall. The tube is then bent into the initial shape of the desired part.
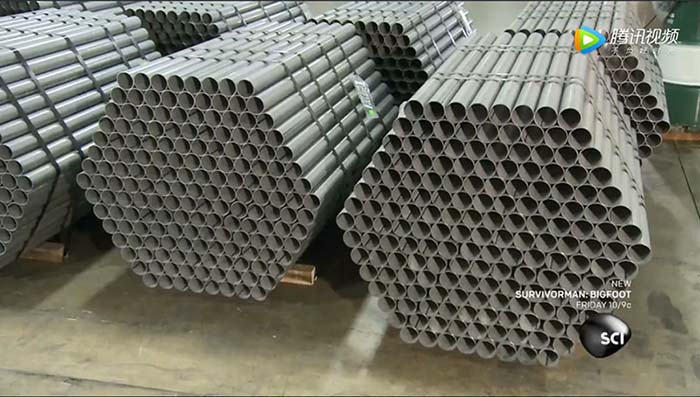
The machine’s hydraulic system needs to generate nearly 9 tons of pressure to bend the steel pipe.
After multiple bends, the part is formed into its initial shape.
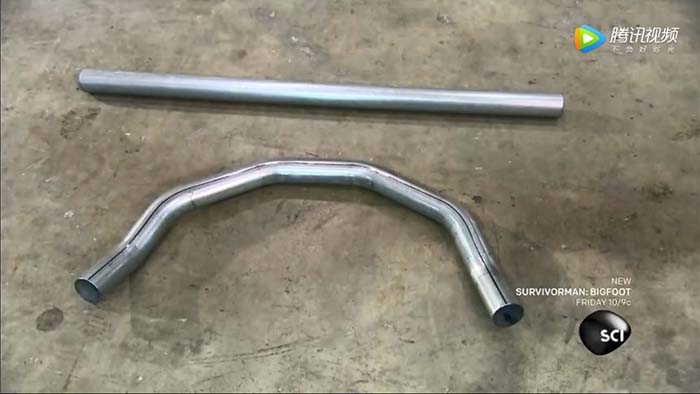
Step 2
Before hydroforming, robots place the steel tubes in pre-forming equipment. A pre-forming press further shapes the tube in preparation for subsequent hydroforming.
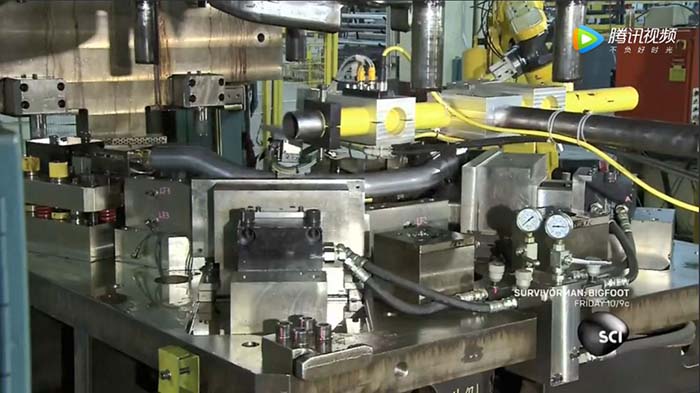
After passing the pre-forming process, we can clearly see the difference in the shape of the pipe before and after forming.
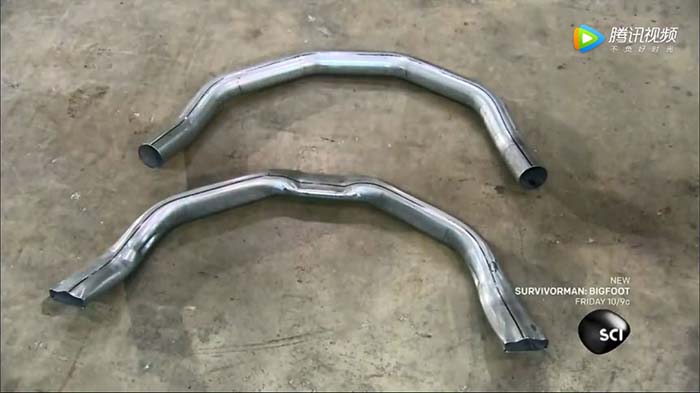
Step 3
The robot will place the preformed steel pipe into the mold cavity on the hydraulic press machine.
Hydraulic press equipment fills the inside of the tube with liquid and seals both ends of the tube. After the equipment is molded, the water pressure is increased to 20,000 psi. The high pressure inside the tube forces the material to fit into the mold cavity, forming the complex shape required.
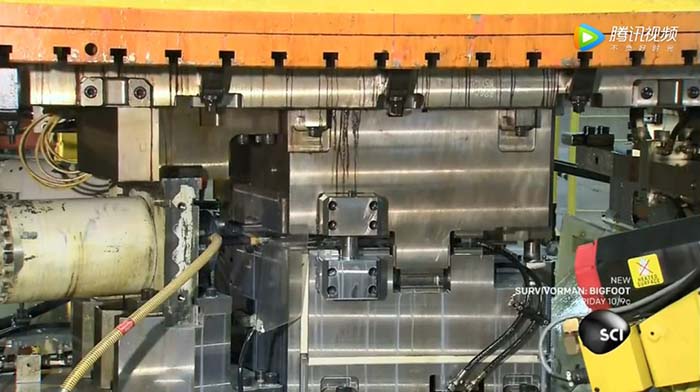
After the job is complete, the robot removes the final formed part from the mold. The hydraulic press can even punch holes in the part at the same time, making it easier to use subsequent screws and bolts.
Step 4
The robot then transfers the part to a cutting machine, which splits it in half. Two symmetrical left and right suspension components are produced.
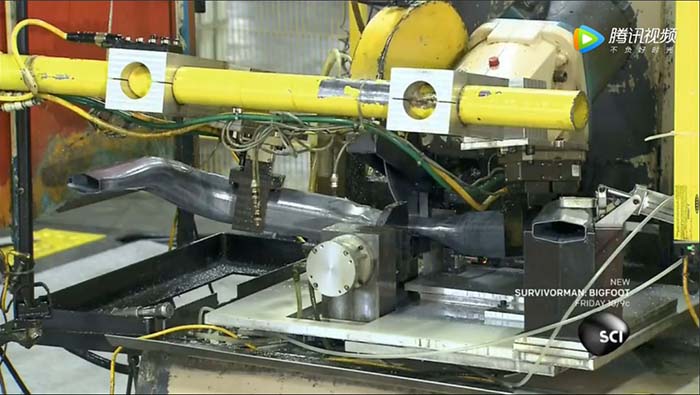
Step 5
After forming, a sharp edge is left on the tube end of the part. So workers use handheld grinders to smooth them. The parts are then inspected by placing them in specially designed verification equipment.
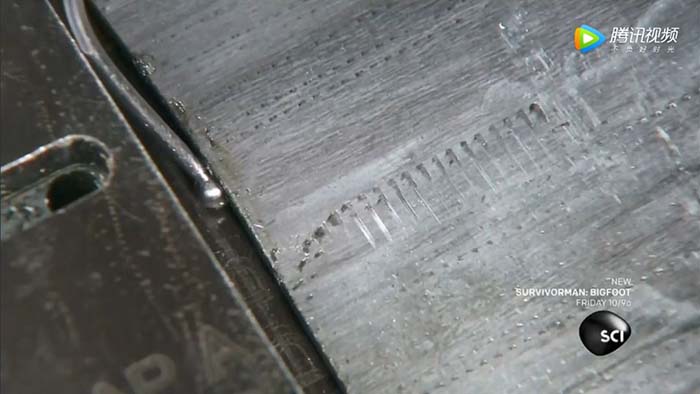
Only if the parts pass inspection are they shipped to the assembly plant.
Workers then place these parts and adjacent suspension parts in assembly jigs. They are welded together by an automated welding machine.
Finally, workers will position and weld the next component to the rear suspension unit.
Once the coating has dried, automated equipment installs sprue bushings for the suspension. Bushings are made of rubber or polyurethane. It is between two metal parts and is mainly used to absorb vibration and reduce noise.
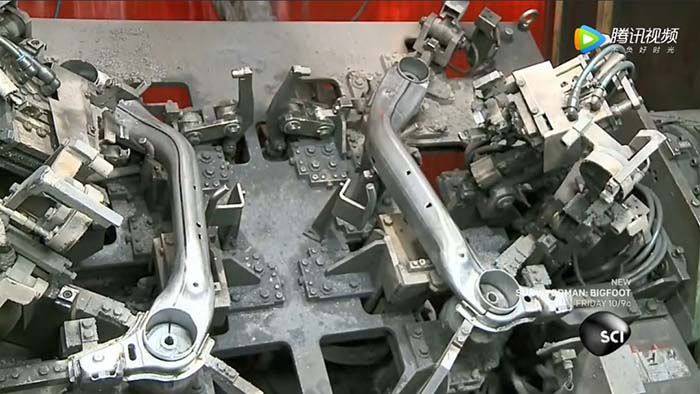
Finally, workers will load the finished parts into shipping racks for shipment to the auto plant.
On a factory assembly line, workers install springs and shock absorbers. They also installed supports, wheels, and brakes. Finally, the entire assembly unit is installed on the vehicle.
Such suspension components were once made from multiple parts using a stamping process. Then weld them together. But today, the same parts can be realized by hydroforming from a single steel tube.
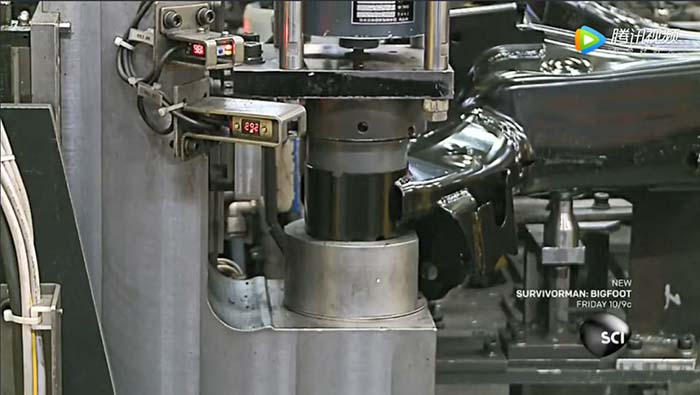
A complete steel pipe will be stronger than a welded piece, so a lighter material can be used instead. This allows car manufacturers to produce integrally formed chassis parts that were previously impossible with traditional stamping techniques and reduce vehicle weight.
Advantages of Zhengxi’s Metal-forming Hydraulic Press
1) Overall casting structure, good rigidity, high compressive strength, small deformation, long life, and low noise.
2) The independently developed embedded software platform has different forming modes and algorithms according to the forming requirements of different materials. This metal forming machine has data acquisition, automatic pressure and temperature compensation, and automatic comparison and correction of displacement accuracy.
3) Programming control, with feedback and automatic gain control, high working accuracy.
4) The main accessories are all imported brand-name products, which reduces the maintenance rate and increases the service life of the equipment.
5) The safety factor is very high. Both the main cylinder and the booster cylinder are equipped with limit switches and are equipped with safety photoelectric protector devices and motor circuit protection.
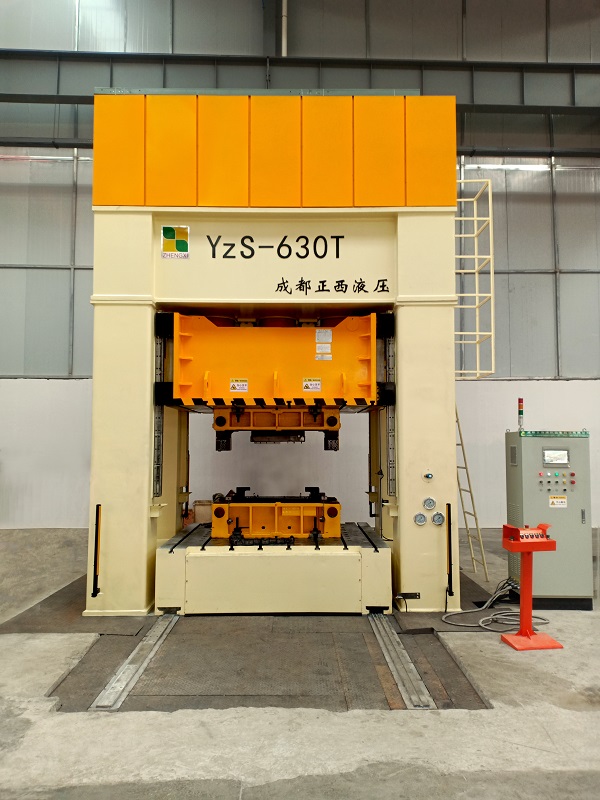
Below are some examples of products developed for customers using our advanced hydraulic press:
Motor vehicle exhaust pipe case:
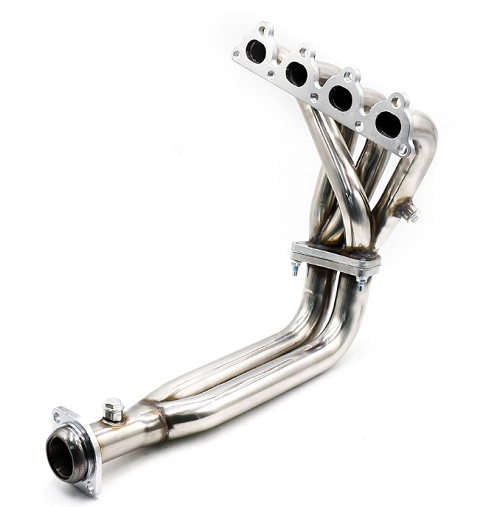
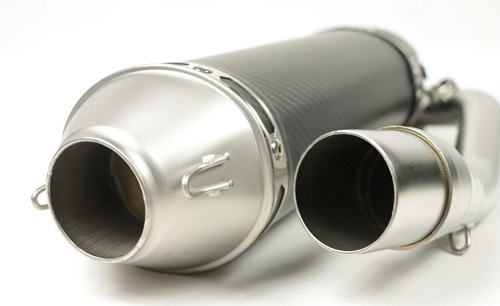
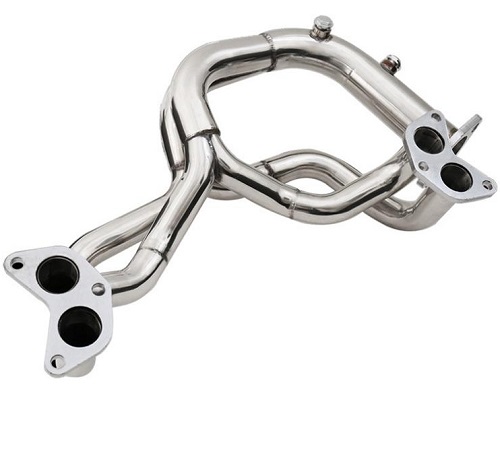