Composite manhole covers, also known as resin manhole covers, or polymer fiberglass manhole covers, are a new type of environmentally friendly covers. It uses fiber-reinforced thermosetting composites based on unsaturated polyester resin, also known as bulk molding compound (DMC), as a raw material. Made using compression molding technology.
The composite manhole cover adopts high temperature and high-pressure one-time compression molding technology, which has a high degree of polymerization, high density, and good impact resistance and tensile strength. It has the advantages of wear resistance, corrosion resistance, no rust, no pollution, and maintenance-free.
Table of Content:
- Advantages of Composite Manhole Covers
- The Production Process of Composite Manhole Cover
- Classification of Composite Manhole Covers
- Making Composite Manhole Cover with Composite Hydraulic Press
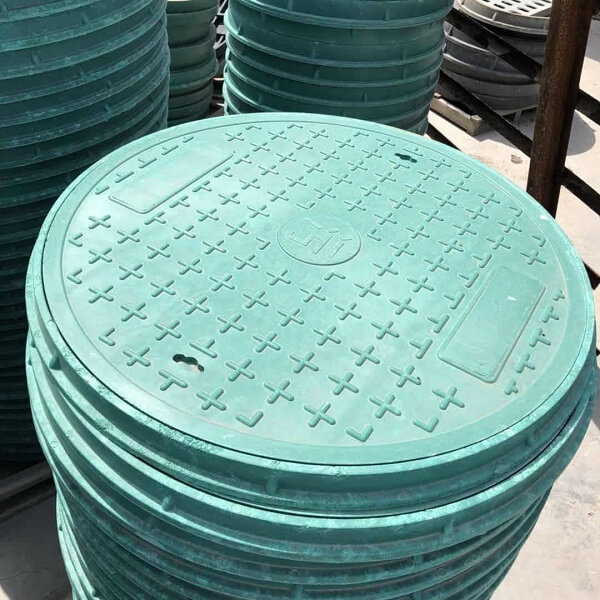
Advantages of Composite Manhole Covers
- Strong anti-theft performance. Manufacturers of composite manhole covers generally use unsaturated resin, glass fiber and other materials to produce manhole covers, which are compounded through special production processes. It is molded once at high temperature, and the product has no recycling value, and the steel bars cannot be extracted.
- Long service life. The use of high-performance resin, glass fiber, and special production process formula ensures the penetration of the composite manhole cover in the glass fiber, greatly enhancing the bonding force between the two. Under the action of cyclic load, the material will not be damaged internally, thus ensuring the service life of the product. Effectively put an end to the disadvantages of poor adhesion.
- High temperature/low-temperature resistance, good insulation performance, and strong corrosion resistance. The product is corrosion-resistant, non-toxic, and harmless. No metal additives. It can be used in complex, changeable, harsh, and demanding places.
- Beautiful and practical, high grade. According to the needs of high-end customers, complex logos and multiple colors can be made on the same manhole cover appearance. The patterns are delicate and the colors are bright and distinct. And it can be made into various imitation stone surfaces and colors according to customer needs.
- Strong carrying capacity. The bottom adopts a special design structure. The continuously reinforced fiber yarn used ensures that the fiber yarn and glass fiber cloth are integrated from the material so that the product has a certain bearing capacity. It has high compressive, bending, and impact strength and toughness. After long-term use, the composite manhole cover will not be crushed or damaged.
- Environmental protection, non-slip, low noise. The manhole cover does not slip and has no ear-piercing noise and pollution after being rolled by the car.
- Strong weather resistance. FRP composite manhole covers can be used normally in an environment of -50℃~+300℃ through scientific formula, advanced technology, and perfect technical equipment.
- Easy to use and light in weight. The weight of the composite manhole cover is only about one-third of that of cast iron, which is convenient for transportation, installation, and emergency repair, and greatly reduces the labor intensity.
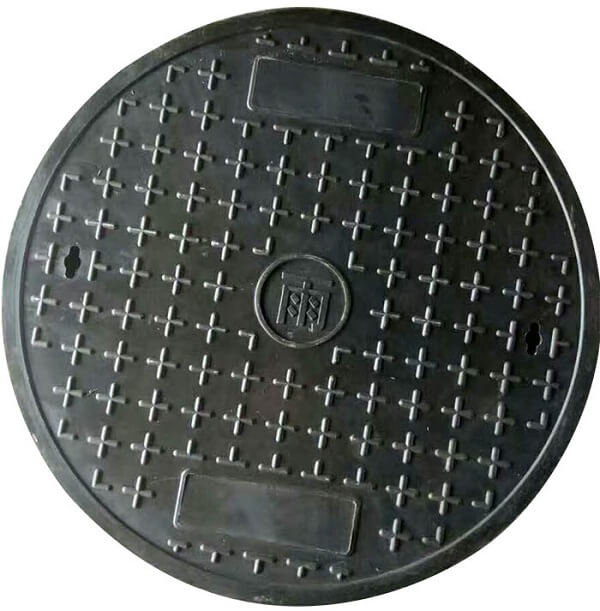
The Production Process of Composite Manhole Cover
FRP composite manhole cover is a manhole cover made of unsaturated polyester resin as raw material, glass fiber as reinforcement material, and certain fillers. Due to different processes, different structural materials, and different reinforcing materials, the performance of the composite manhole cover products is also very different. The process of producing FRP manhole covers generally includes:
(1) Resin transfer molding process. Due to the high resin content, the manufactured manhole cover is not suitable for use on the roadway due to insufficient bearing capacity.
(2) Hand lay-up process. The production efficiency is slow, not suitable for large-scale production, and has no competitive advantage.
(3) Molding process. The molding process is layered composite compression molding under a certain temperature and pressure. The product structure is relatively dense, and different materials are used in different parts of the manhole cover. The lower part of the manhole cover is reinforced with continuous fiber to ensure its bearing capacity. Fillers are used in the middle to improve the product’s resistance to deformation and reduce production costs. The upper part uses materials with higher hardness and good wear resistance to improve the compression resistance and wear resistance of the upper part of the product. There are special composite hydraulic presses to press composite manhole covers.
FRP manhole covers have been gradually promoted due to their advantages of light material, high strength, fatigue resistance, corrosion resistance, not easy to brittle damage, and easy processing and molding.
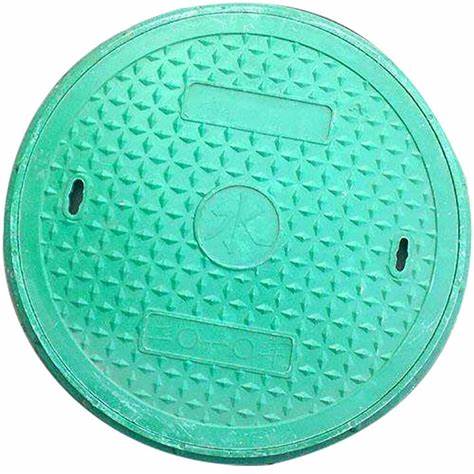
Classification of Composite Manhole Covers
Composite manhole covers can be divided into BMC composite manhole covers and SMC composite manhole covers according to market demand, manufacturing process, and materials.
BMC Manhole Cover
BMC (DMC) material is a bulk molding compound. Its main raw materials are GF (chopped glass fiber), UP (unsaturated resin), MD (filler), and various additives that are fully mixed into a dough-like prepreg. Because BMC bulk molding compound has excellent electrical properties, mechanical properties, heat resistance, and chemical corrosion resistance, and adapts to various molding processes, BMC manhole covers are widely used.
SMC Manhole Cover
SMC composites are sheet molding compounds. The main raw materials are composed of GF (special yarn), UP (unsaturated resin), low shrinkage additive, MD (filler), and various auxiliary agents. SMC composite materials and their SMC molded products have excellent electrical insulation properties, mechanical properties, thermal stability, and chemical corrosion resistance. Therefore, the application range of SMC manhole covers is quite common. The current development trend is that SMC manhole covers replace BMC manhole covers.
BMC composite manhole covers do not require high load-bearing and are usually used in green belts in residential areas. SMC composite manhole covers are suitable for all places.
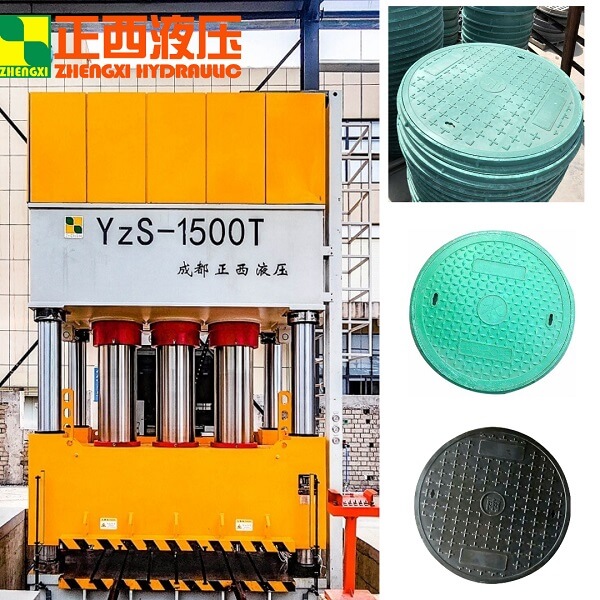
Making Composite Manhole Cover with Composite Hydraulic Press
Whether it is to produce BMC manhole covers or SMC manhole covers, our composite material hydraulic presses can be used to press the products.
BMC & SMC manhole cover making machine adopts a three-beam and four-column structure. High-quality castings are selected, with high strength and good stability. It uses mold electric heating, the heating temperature is about 140°C-150°C, and the holding time is about 3 minutes. The equipment, curing time, pressure, and speed are all in line with the process characteristics of SMC/BMC materials.
Our composite material molding machine can be configured with an in-mold core-pulling control system and a preset in-mold ejection control system, which can realize a series of actions such as rapid descent, segmental compaction, segmental deflation, work, pressure maintaining, slow mold opening, rapid return, slow demoulding, rapid ejection, ejection stop, and rapid return. The temperature can be controlled at multiple points.
Zhengxi is a famous manufacturer of hydraulic presses, providing professional composite hydraulic presses. If you have any needs, please contact us.