Multidirectional forging is a manufacturing process that uses multi-directional pressure to plastically deform metal. Its purpose is to improve the mechanical properties of the material, especially to optimize the density and microstructure of the part through uniform metal flow. In the multi-directional forging process, the design of the die needs to have a certain complexity and high precision to ensure that the metal is evenly stressed in multiple directions, thereby achieving higher material properties.
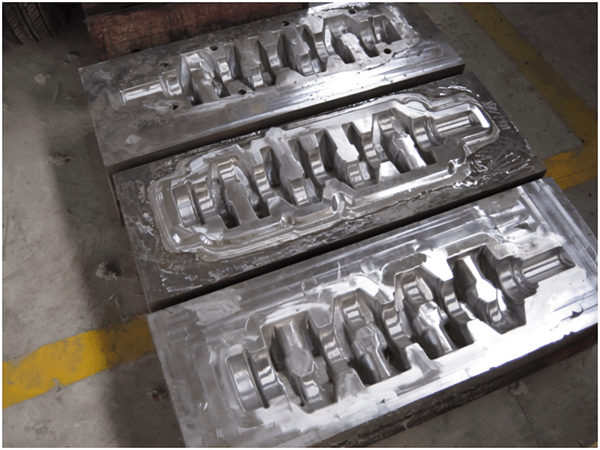
Types of Die Structures for Multi-directional Die Forging
According to the different parting methods, there are three basic structural forms, namely vertical parting die structure, horizontal parting die structure and compound parting die structure.
1. Horizontal parting die structure
The parting surface of this type of die structure is parallel to the table surface of the press. The upper die and the lower die are connected to the movable crossbeam and the lower crossbeam table of the multi-directional die forging press, respectively, through T-shaped bolts. The horizontal punch is connected to the horizontal cylinder piston of the multi-directional die forging press. The vertical punch is connected to the vertical cylinder piston of the multi-directional die forging press.
When installing the die, ensure that the center line of the horizontal punch coincides with the center line of the left and right holes of the upper and lower dies, and the center line of the vertical punch coincides with the center line of the upper die hole. After the blank is placed in the cavity of the lower die, the upper and lower dies are tightened through the upper crossbeam, and the upper punch and the horizontal punch extrude the blank through the vertical working cylinder and the horizontal working cylinder, respectively.
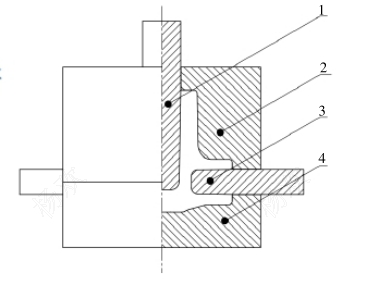
1–Vertical punch 2–Upper die 3–Horizontal punch 4–Lower die
2. Vertical split die structure
The split surface of this type of die structure is perpendicular to the multi-directional die forging press work surface. The left and right dies are connected to the connecting rod through hexagonal screws. The connecting rod is connected to the horizontal working cylinder piston. The vertical punch is connected to the vertical working cylinder piston. The left and right die-moving table is connected to the multi-directional forging work surface through T-bolts.
The left and right die move left and right on the moving pad. When the vertical punch returns after forging, the moving pad makes the left and right die and stays on the moving pad through the moving pad dovetail groove. The horizontal working cylinder closes the left and right dies, and the closing load is provided. After the left and right dies are closed, the blank is placed in the die cavity, and the vertical punch squeezes the blank to fill the die cavity with metal.
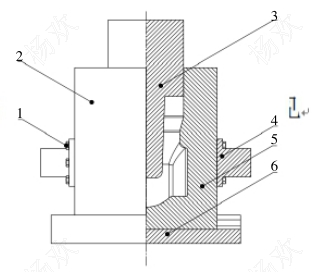
1–Hexagonal screw 2–Left die 3–Vertical punch 4–Connecting rod 5–Right die 6–Moving pad
3. Compound split die structure
The compound split die structure has two split surfaces. One split surface is parallel to the multi-directional die-forging press work surface, and the other split surface is perpendicular to the multi-directional die-forging press work surface. Compared with the horizontal split die, the compound split die can forge valve body forgings with main flanges. Compared with the vertical parting die, the parting surface of the composite parting die perpendicular to the worktable surface is much smaller than that of the vertical parting die, which greatly reduces the clamping load of the composite parting die in the left and right directions. The clamping load of the composite parting die in the up and down directions can be provided by the clamping cylinder of the multi-directional die forging press. Therefore, the composite parting die structure can forge a much wider range of products on the same press than the vertical parting die.
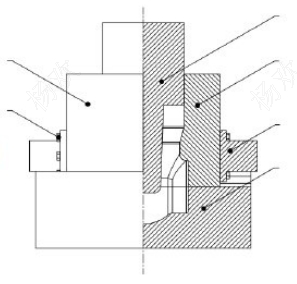
Characteristics of Multi-directional Die Forging Die
Die structure design: Multi-directional die forging dies usually consist of multiple movable parts that can apply pressure in different directions, usually using multiple different pressing directions (such as horizontal, vertical or oblique). These dies may include multiple independent die blocks that are operated by hydraulic, mechanical and other means.
- High strength and wear resistance: Since the metal flow is subjected to multi-directional forces during multi-directional die forging, the die needs to have very high strength and wear resistance. High-strength alloy steel or other wear-resistant materials are often used to make dies to extend the service life of the die.
- Temperature control system: During multi-directional die forging, metal often needs to be plastically deformed under high-temperature conditions, so the die must be equipped with an effective temperature control system, such as cooling channels or heating systems, to maintain the appropriate working temperature. This is crucial to improving the life of the die and ensuring the quality of the product.
- Complex geometry design: Due to the complex geometry of die forgings, the die usually requires precise processing and design to ensure that the metal can flow evenly under multidirectional forces. The die surface also requires special finishing to reduce the metal’s friction.
- High-precision machining: The design and machining of multi-directional forging dies require extremely high precision. Every detail of the die directly affects the quality of the finished product, especially in the manufacturing process of parts with complex shapes, where precision and durability are key.
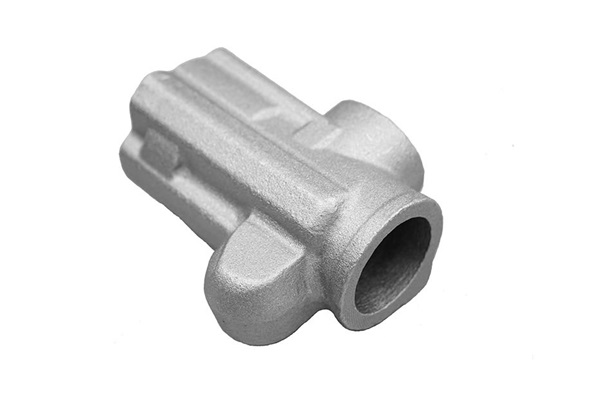
Damage Forms of Multi-directional Die Forging Dies
Compared with ordinary die forging, multi-directional die forging forms forging mostly once. When multi-directional die forging forms forgings, the metal flows violently, and the wear on the die and punch is more serious. Common failure forms of multi-directional die forging dies are cracks, collapse, and punch fracture.
1. Cracks
When multi-directional die forging forms valve body forgings, during the vertical perforation process, the blank metal flows to both sides of the forging, and the friction load between the metal and the die surface is large. The damage to the die during the metal flow process is more serious. At the same time, during the forging process, due to the continuous cooling of the die, the die surface constantly changes between hot and cold, and cracks are formed after the die is in service for a long time.
2. Collapse
When multi-directional die forging forms the valve body, after the upper die is closed, the blank metal flows into the upper die cavity. During the vertical punch perforation process, the metal flowing into the upper die cavity is squeezed down by the vertical punch. Under such repeated actions, the metal collapses the sharp edges of the upper die cavity.
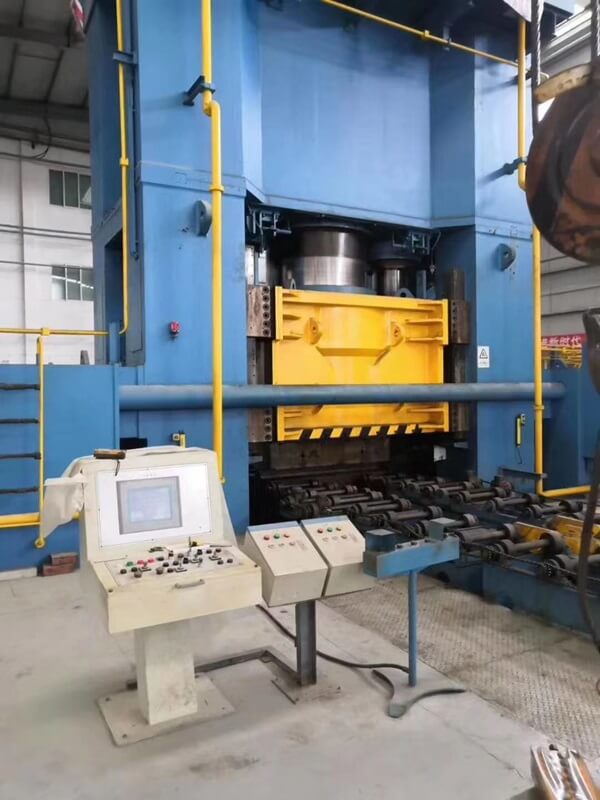
3. Punch fracture
When the valve body forging is formed by multidirectional die forging, during the vertical perforation process, the metal flow trend to the two sides of the forging is inconsistent, and the vertical punch is subjected to an eccentric load. After the vertical punch has been in service for a long time, it breaks.
Zhengxi is a famous forging press manufacturer in China that provides professional press knowledge and high-quality hydraulic forging presses. If you have any needs, contact us!