Hydroforming refers to a plastic processing technology that uses liquid or mold to shape a workpiece. The pressure of the liquid replaces the rigid punch or die to stamp the sheet. This cuts tooling costs and machining time in half. Moreover, the liquid can be used as a convex mold to form many complex parts that cannot be formed by rigid molds.
There are many stamping processes that can be performed in hydroforming, such as bending, deep drawing, bulging of flat blanks, bulging of space blank shapes, etc. It can form various complex parts, such as bellows. And it has the advantages of good surface quality, reduced process, simplified mold, and no special stamping equipment.
Table of Contents
- Classification of Hydroforming
- Main Features of Modern Hydroforming Technology
- Advantages of Hydroforming
- Disadvantages of Hydroforming
- Application of Hydroforming Process
1. Classification of Hydroforming
According to the different liquid media used, hydraulic forming can be divided into water hydraulic forming and oil hydraulic forming. The medium used in water hydroforming is pure water or an emulsion composed of water plus a certain proportion of emulsified oil. The medium used in oil hydraulic forming is hydraulic transmission oil or machine oil.
According to the different blanks used, hydroforming can be divided into three types: pipe hydroforming, sheet hydroforming, and shell hydroforming. Sheet and shell hydroforming uses lower forming pressures. The pressure used in pipe hydroforming is relatively high, also known as internal high-pressure forming.
The medium used in sheet metal hydroforming is mostly hydraulic oil, and the maximum forming pressure generally does not exceed 100MPa. The medium used in shell hydroforming is pure water, and the maximum forming pressure generally does not exceed 50MPa. The medium used in internal high-pressure forming is mostly emulsion. And the maximum forming pressure used in industrial production generally does not exceed 400MPa.
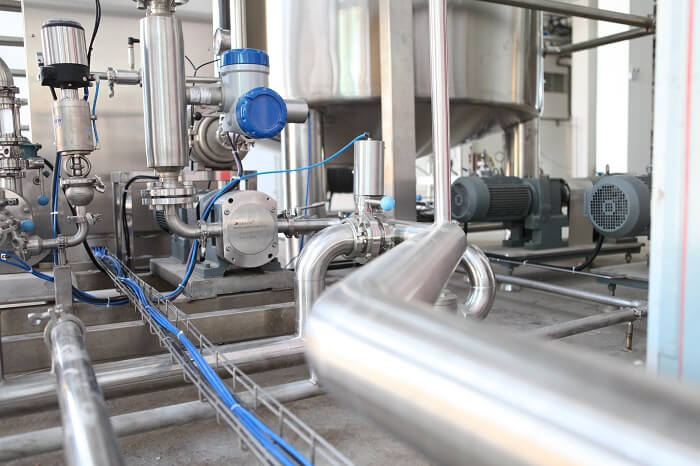
Internal high-pressure forming
The main feature of the internal high-pressure forming technology is that it can integrally form a hollow part with a special-shaped cross-section whose axis is a two-dimensional or three-dimensional curve. From the initial circular section of the pipe, it can be shaped into a rectangular, trapezoidal, elliptical, or other special-shaped closed section. Internal high-pressure forming is an advanced manufacturing technology developed to adapt to the lightweight structure of transportation tools such as automobiles and aircraft.
Sheet metal hydroforming
Sheet metal hydroforming is an advanced metal-forming process. This process has the characteristics of low mold cost, short mold manufacturing cycle, high forming limit, and high forming quality. It is one of the main technology of sheet metal flexible forming.
It is suitable for parts with a high degree of deformation in the aerospace field that requires multi-pass deep drawings, such as fairings and other cylindrical parts with complex surfaces, conical parts, etc. At the same time, it is also suitable for parts with complex profiles in the automotive field, such as automotive lamp reflectors, etc. In addition, sheet metal hydroforming is also suitable for processing many kitchen products, such as stainless steel tableware, containers, hand basins, and other deep parts.
Advantages of sheet metal hydroforming technology:
① Under the pressure of the friction retention effect, a friction retention effect is formed between the sheet and the punch. This can enhance the bearing capacity of the sheet material in the fillet area of the punch, increase the forming limit, and reduce the forming times.
②Fluid lubrication effect. The liquid pressure in the liquid chamber makes the sheet close to the punch, and the liquid forms fluid lubrication between the upper surface of the die and the lower surface of the blank. This can reduce the scratches on the surface of the parts so that the parts have good quality, high dimensional accuracy, and uniform wall thickness distribution.
③Suppresses wrinkling of curved surface parts. Due to the reverse hydraulic action under the formed sheet, the suspended area of the curved surface parts in the die hole is eliminated, so that the blank is close to the punch and forms a “convex stem”. This reduces the “suspension section” when deep-drawing complex parts such as hemispheres and cones, and effectively controls the occurrence of defects such as inner wrinkles of materials.
④ It is possible to process automotive sheet metal forming workpieces with complex curved surfaces with reduced molds and no molds. Change the multi-stretch forming process of the traditional rigid forming process into a one-time flexible forming to improve the surface accuracy and internal strength of the formed part.
It can save a lot of manpower, material resources and time for mold design, manufacture, and debugging. Especially in the production of large-scale plate forming with multiple varieties and small batches, it can overcome the limitation of cost and time, and make the product update faster and faster.
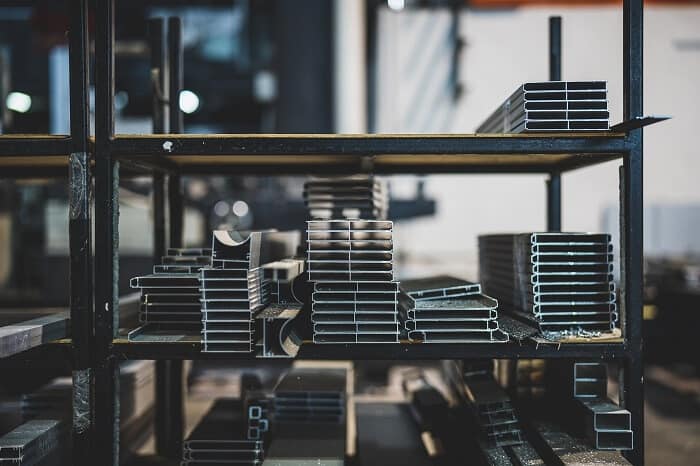
Shell hydroforming technology
Shell hydroforming is to use of a closed polyhedral shell of a certain shape as a preform. After the closed polyhedral shell is filled with liquid, the closed polyhedral shell is pressurized by the liquid medium. Under the action of internal pressure, the shell produces plastic deformation and gradually tends to the final shell shape. The final shell shape can be spherical, ellipsoidal, toroidal, or other-shaped shells.
Main advantages of shell hydroforming:
① No need for molds and presses. From a mechanical point of view, the principle of this technology is to use the internal pressure of the integrally closed shell to maintain a balanced force by itself. That is to say, the integrally closed shell itself is not only a deformable body but also a carrier to realize the balance of the force system. Thereby realizing forming large-scale casing without a press machine and mold.
②It is easy to change the shell wall thickness and diameter. Since there is no need for molds and presses, for the required diameter and thickness of the shell, as long as a reasonable preform is designed to close the multi-faced shell, it can be directly press-formed.
③The product has high precision. Since the shell manufacturing process is changed from the traditional “forming first and then welding” to “welding first and then forming”, the forming process is to correct the deformation of the previous welding. And the dimensional accuracy of the final product is high.
④Reduce costs and shorten the manufacturing cycle. Since molds and presses are not used, molding time and mold costs are saved.
The disadvantages of shell hydroforming:
① Since the technology is “welding first and then forming”, the weld seam of the closed multi-faced shell is subject to certain plastic deformation during the forming process. If there is a problem with the quality of the weld, it will cause cracking and cause the entire shell to be scrapped. This problem is more serious for thick plate and low alloy steel. Therefore, controlling the welding quality is the key.
②For large shells, the support foundation for the forming process is difficult and expensive.
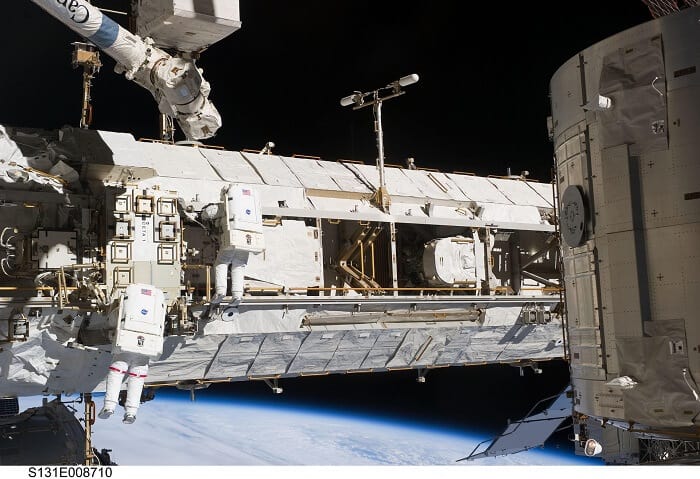
Main Features of Modern Hydroforming Technology
Only a die or punch is required. The liquid medium is correspondingly used as a punch or die, saving half of the mold cost and processing time. And the liquid can be used as a punch to form many complex parts that cannot be formed by a rigid punch. Shell hydroforming does not use any molds, so it is also called dieless hydroforming.
As a force transmission medium, liquid has real-time controllability. The pressure can be precisely controlled according to the given curve through the hydraulic closed-loop servo system and the computer control system. Make sure that the process parameters are within the set values and can be adjusted over time. This greatly increases process flexibility.
Advantages of Hydroforming
For hollow structural parts with variable cross-sections, the traditional manufacturing process is to stamp two halves first and then weld them into a whole. While hydroforming can integrally form hollow structural parts that vary along the cross-section of the member at one time. Compared with the stamping and welding process, the hydroforming technology and process have the following main advantages:
1. Reduce quality and save materials. For typical parts such as automobile engine brackets and radiator brackets, hydroformed parts are 20% to 40% lighter than stamped parts. For hollow stepped shaft parts, the weight can be reduced by 40% to 50%.
2. Reduce the number of parts and molds, and reduce mold costs. Hydroformed parts usually only need one set of molds, while stamping parts mostly require multiple sets of molds. The number of hydroformed engine bracket parts was reduced from 6 to 1, and the number of radiator bracket parts was reduced from 17 to 10.
3. It can reduce the amount of welding for subsequent machining and assembly. Taking the radiator bracket as an example, the heat dissipation area has increased by 43%, the number of solder joints has been reduced from 174 to 20, the number of processes has been reduced from 13 to 6, and the productivity has increased by 66%.
4. Improve strength and rigidity, especially fatigue strength. For example, in a hydroformed radiator bracket, its rigidity can be increased by 39% in the vertical direction and 50% in the horizontal direction.
5. Reduce production costs. According to the statistical analysis of applied hydroforming parts, the production cost of hydroforming parts is 15%-20% lower than that of stamping parts on average, and the mold cost is reduced by 20%-30%.
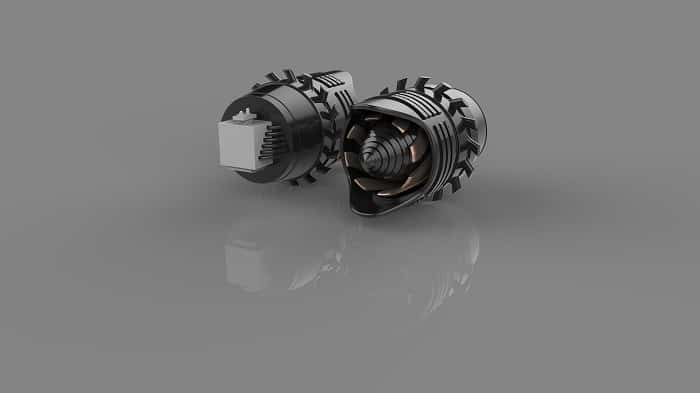
Disadvantages of Hydroforming
1) The manufacturing precision of hydraulic components is high. Due to the high technical requirements of the components and the difficulty in assembly, the use and maintenance are relatively strict.
2) It is difficult to realize constant ratio transmission. The hydraulic transmission uses hydraulic oil as the working medium, and leakage is inevitable between relatively moving surfaces. At the same time, the oil is not absolutely incompressible. Therefore, it is not suitable for applications where the transmission ratio is strict, such as the transmission system of thread and gear processing machine tools.
3) Oil is affected by temperature. Since the viscosity of oil changes with temperature, it is not suitable to work in a high or low-temperature environment.
4) Due to the use of oil pipes to transmit pressure oil, the pressure loss is relatively large, so it is not suitable for long-distance transmission of power.
5) The air mixed in the oil will easily affect the working performance. After the air is mixed into the oil, it is easy to cause crawling, vibration, and noise, which will affect the working performance of the system.
Application of Hydroforming Process
Suitable materials for the hydroforming process include carbon steel, stainless steel, aluminum alloys, copper alloys, and nickel alloys. In principle, all materials suitable for cold forming are suitable for hydroforming. The hydroforming process is mainly used for auto parts factories, electronics factories, electrical appliances factories, heat treatment factories, vehicle parts factories, gear factories, and air-conditioning parts factories.
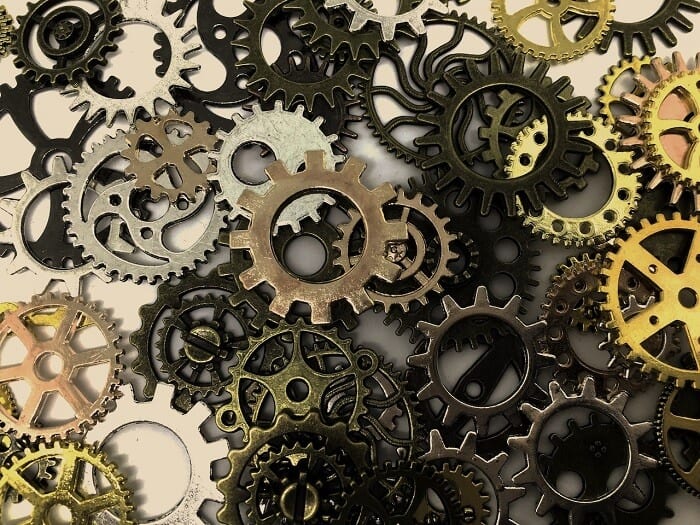