The compression molding equipment produces thermosetting plastics through heating, pressurizing, curing, demolding and other steps. The core equipment is the hydraulic press and mold. The temperature, pressure and time need to be precisely controlled. At the same time, it can be equipped with preheating and post-processing equipment to optimize the process. The following is a detailed introduction:
1. Core equipment
1) Hydraulic press
Function: The hydraulic press is the main equipment for compression molding. It is responsible for applying pressure to the plastic through the mold, opening the mold and ejecting the product at the same time.
Type: According to the different pressing methods, hydraulic presses can be divided into upper-pressure type and lower-pressure type. The oil cylinder of the upper pressure hydraulic press is located at the top, and the movable crossbeam is pushed from top to bottom by the oil cylinder piston; the oil cylinder of the lower pressure hydraulic press is located at the bottom, and the lower crossbeam is pushed from bottom to top by the oil cylinder piston.
Specifications: The specifications of the hydraulic press are expressed in nominal tonnage. Common ones are 40t, 63t, 100t, 160t, 200t, etc. Multilayer presses can reach more than 1,000 tons.
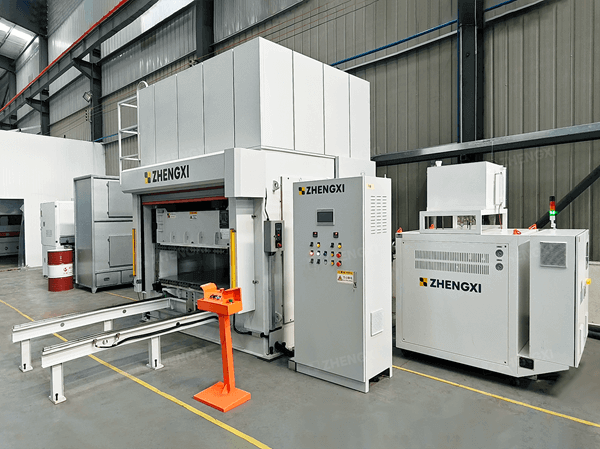
2) Mold
Function: The mold is a key component of compression molding and determines the shape and size of the product.
Type: Molds can be divided into open, semi-overflow and closed types according to their structural forms. Semi-overflow molds are often used for compression molding of thermosetting plastics to control the flow and overflow of materials.
Material: The mold is usually made of steel and must have sufficient strength and wear resistance to withstand repeated use under high temperature and high pressure.
Auxiliary equipment
1) Preheating equipment:
Function: Preheating equipment is used to heat plastic raw materials before molding to improve their fluidity and curing uniformity and reduce the internal stress of the product.
Type: Preheating equipment includes hot plate heating, oven heating, infrared heating and high-frequency heating.
2) Mold temperature controller:
Function: The mold temperature controller is responsible for controlling the temperature of the mold to ensure the stability of the heat transfer conditions from the mold to the material in the mold cavity, thereby affecting the melting, flow and curing process of the material.
Type: The mold temperature controller can be divided into oil-type mold temperature controllers and water-type mold temperature controllers according to the different heating media.
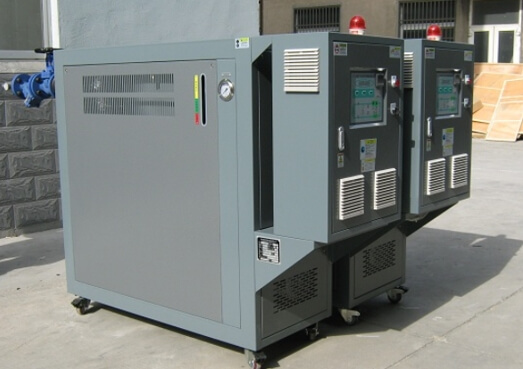
3) Post-processing equipment:
Function: For some products that require post-processing, such as the post-baking process of thermosetting plastics, post-processing equipment, such as ovens, is required.
Purpose: Post-processing can further improve the performance and stability of the product, eliminate residual stress, and prevent product deformation and cracking.
3. Production process
- Raw material preparation: Select appropriate thermosetting plastic raw materials and pre-treat them according to the requirements of the product, such as crushing, mixing, drying, etc.
- Mold design and manufacturing: Design and manufacture the corresponding mold according to the shape, size and performance requirements of the product.
- Preheating and feeding: Preheat the mold to an appropriate temperature and add the pre-treated plastic raw materials into the mold. Preheating can improve the fluidity and curing uniformity of the plastic.
- Mold closing and pressurization: Close the mold and apply a certain pressure to ensure that the plastic raw materials are evenly distributed in the mold. The size of the pressure and the application time need to be adjusted according to the type of plastic and the requirements of the product.
- Heating and curing: Heat the plastic raw materials in the mold to make them react chemically and gradually solidify. The temperature and time need to be controlled during the curing process to ensure the performance and quality of the product.
- Cooling and demoulding: After the product is completely cured, cool the mold to room temperature and take out the product. The cooling process needs to be carried out slowly to prevent the product from cracking due to stress concentration.
- Post-processing: For some products that require post-processing, such as heat treatment to eliminate residual stress.
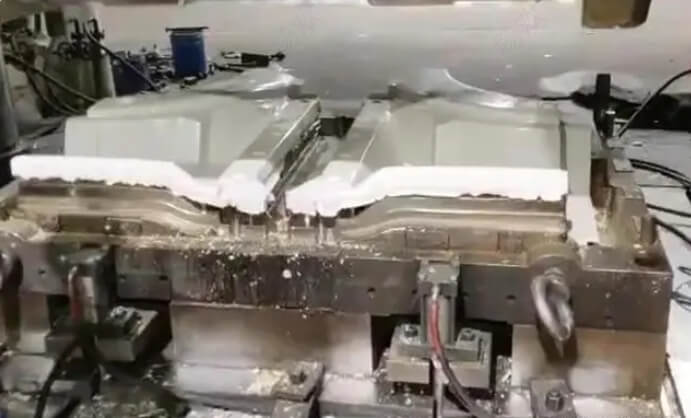
As a professional composite molding press manufacturer in China, Zhengxi provides high-quality plastic compression molding machines. If you have any needs, please contact us.