FRP cooling tower is a kind of efficient cooling equipment. Its tower body is generally made of FRP panels. This makes the tower body have good anti-corrosion performance and have the characteristics of light weight, corrosion resistance, and not easy to damage. Therefore, FRP cooling tower is widely used in the chemical industry, electric power, metallurgy, and other fields. Our cooling tower panel forming machine is designed for one-time compression molding cooling tower plates. With the cooperation of the mold, FRP cooling tower panels that meet the standards can be quickly pressed out.
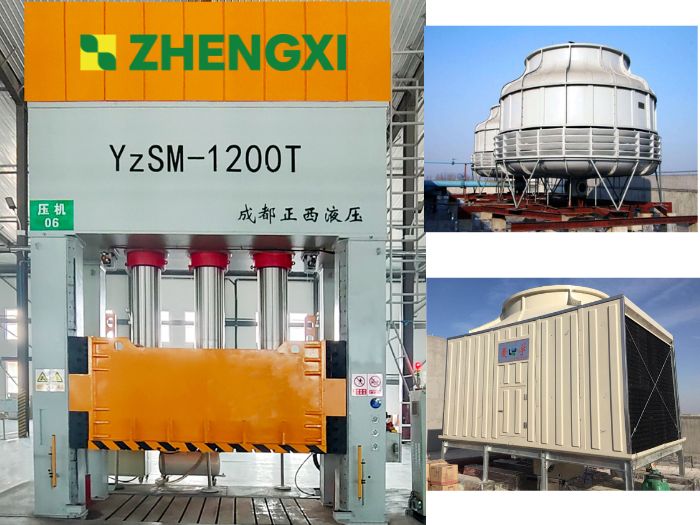
FRP cooling tower panels forming hydraulic press have a variety of structures, including three-beam four-column, and frame types. According to the specifications of the molded cooling tower plate, 1500 tons, 1800 tons, 2000 tons, 3000 tons, 4000 tons, and other four-column hydraulic presses are commonly used.
Features of FRP Cooling Tower Panel Forming Machine:
- Hydraulic control adopts a cartridge valve integrated system. It has stable action, long service life, small hydraulic shock, and reduces connecting pipelines and leakage points.
- The molded FRP cooling tower plate forming hydraulic press adopts a computer-optimized structural design, a three-beam four-column structure, which is simple, economical, and applicable.
- Separate electrical control system, stable operation, intuitive action, and convenient maintenance.
- Through the operation panel selection, two operation processes of fixed stroke and fixed pressure can be realized. And it has functions such as long-term work under pressure.
- The power mechanism and electrical system are arranged separately and centrally controlled by buttons. Manual injection or automatic injection can be realized.
- The working pressure, pressing speed, high-pressure downward and no-load rapid downward, and ejection stroke of the FRP cooling tower panels hydraulic press are controlled by pressure sensors, micro-speed regulating valves, induction sensors, displacement sensors, etc. It can be adjusted according to the pressing process of different products.
- The hydraulic press for molded FRP cooling tower panels adjusts force, time, and stroke parameters on the touch screen through PLC to ensure product quality and high consistency.
- It adopts a four-column slide block structure with a cylinder-driven fast-moving workbench. The ejection device placed outside the four columns cooperates with the mobile workbench to realize mold change and product removal outside the machine.

Advantages of FRP Cooling Tower Plate Forming Hydraulic Press
- The molded FRP cooling tower panel hydraulic press adopts a three-beam multi-column structure. The three beams are welded for aging treatment, and the machine has sufficient rigidity and strength. The operating space is spacious, which is convenient for observation, installation, and adjustment of the mold from all sides. The overall structure is simple and the appearance is beautiful.
- The hydraulic system adopts an integrated plug-in system and a proportional control valve. It can achieve the requirements of large flow, high synchronization accuracy, and large anti-eccentric load capacity. The structure is simple and compact, and the action is sensitive and reliable, which is convenient for fault diagnosis and troubleshooting.
- The slider of the molded FRP cooling tower panel hydraulic press has a high idle speed, which effectively prevents the molded material from pre-curing after entering the mold.
- The speed and pressure of the slider can be adjusted arbitrarily within the specified range of parameters. It has a controllable pre-pressing process to increase the flow rate of the material in the mold and shorten the pressurization time.
- The FRP cooling tower panel forming machine has an automatic exhaust function during the pressing process.
- The slider return has a micro-opening function. After the FRP cooling tower plate is formed, it is slowly separated from the mold to prevent the product from being torn and stretched.
- It has a safety protection device in the form of a light curtain and a hydraulic lock device to prevent the slide from sliding down when installing the mold.
- The hydraulic system is equipped with two sets of in-mold core pulling control systems and a pre-set in-mold ejection control system. It can add functions such as multi-point ejection and air blowing.
- The power system of this machine is placed on the top to reduce the footprint of the machine.
- There are safety guardrails around the upper beam and a spare ladder for easy installation and maintenance.
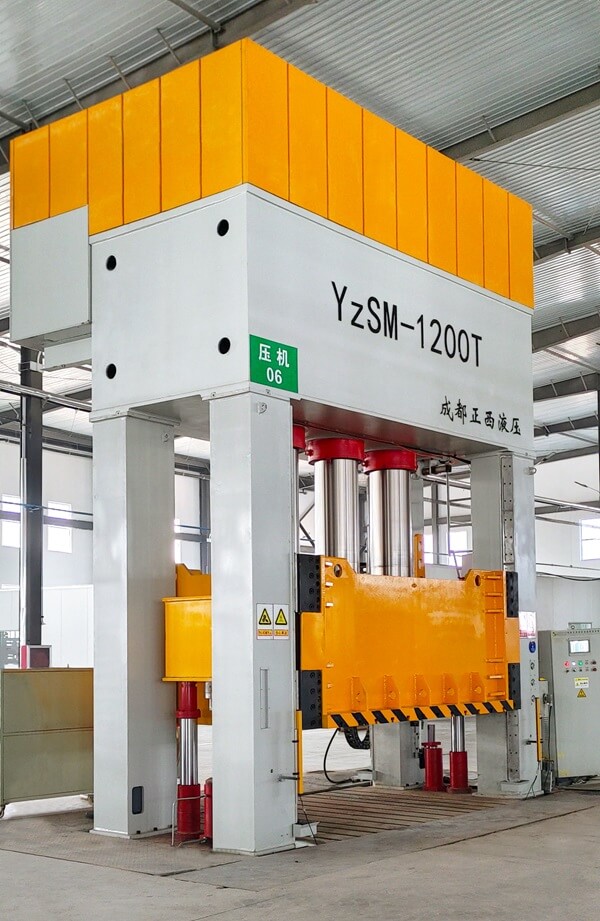
Processing Flow of FRP Cooling Tower Panel Molding Press Machine
First, put the powdered, granular, or fibrous plastic into a mold with a certain temperature. Then close the mold, heat and pressurize it, so that the material is formed and solidified in the mold.
The hydraulic press equipment process works as follows:
The slider moves down quickly – slider moves down slowly and pressurizes – the slider maintains pressure – pressure relief – fast return – the top cylinder returns – return stops (manual blank removal) – the top cylinder pushes out – adding materials – the two-hand button enters the next cycle.
Optional Accessories for FRP Cooling Tower Panel Forming Hydraulic Press:
- Mobile workbench
- Punching buffer device
- Light curtain protection device
- Stroke, pressure, speed digital display, CNC device
- Touch-type industrial display screen
- Hydraulic system heating and cooling device
- Material punching device
- Slider limit valve
- Mold heating and temperature control device
- PLC programmable controller
- Single-cylinder, double-cylinder, and multi-cylinder layouts can be selected according to the process
Finished Product of Molded FRP Cooling Tower Panel Using a Four-column Hydraulic Press :
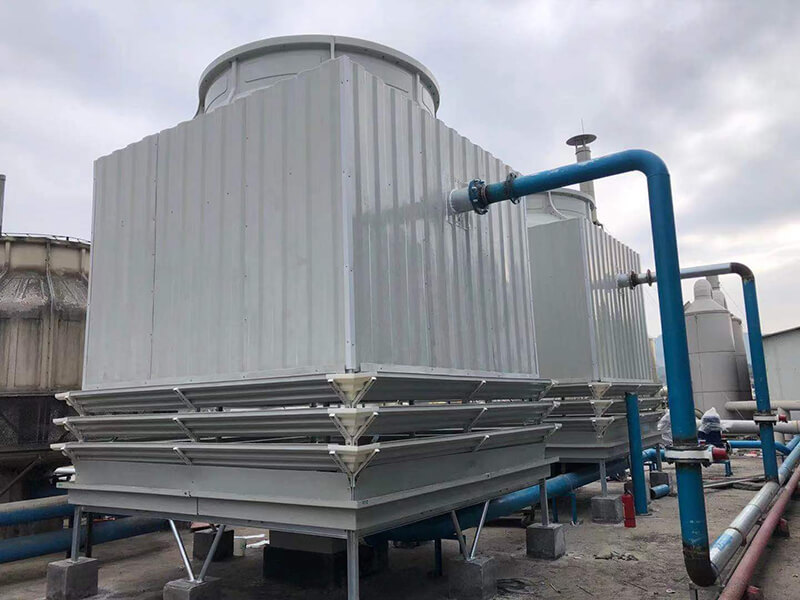
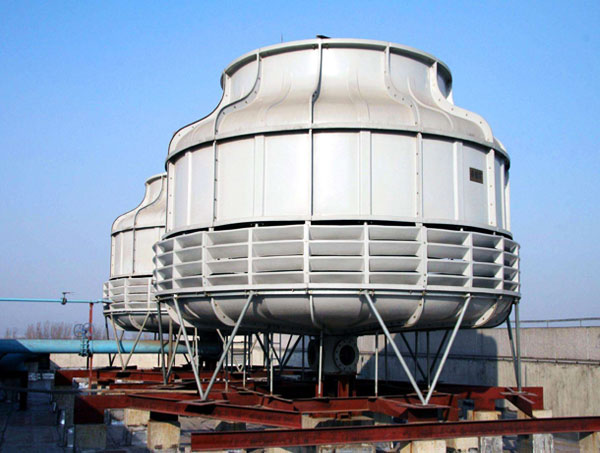
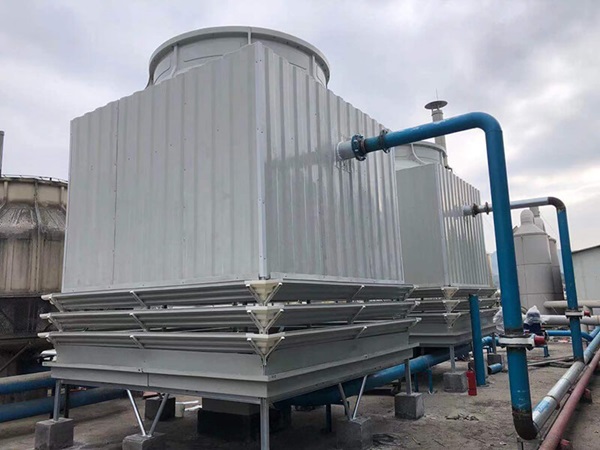