During the use of the hydraulic press, various failures may occur due to improper operation or maintenance. Common faults include action failure, slider crawling, pressure on the slider when it goes down slowly, serious sliding of the slider after parking, and severe lifting of the pressure gauge pointer. When encountering these failures, the cause of the failure must first be checked and then repaired. The common maintenance methods of hydraulic presses mainly include the replacement method, auxiliary method, and empirical method. Let’s take a look.
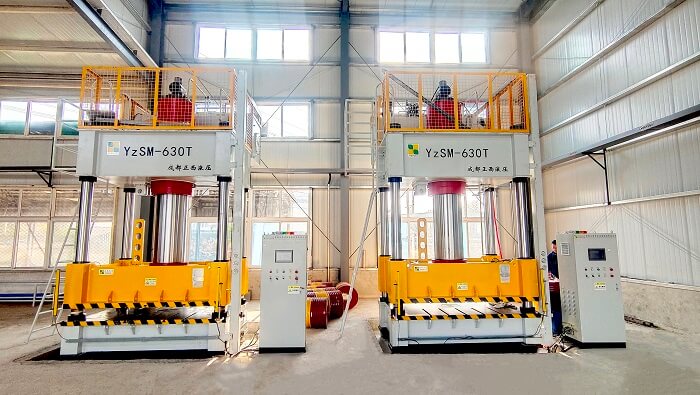
Common Faults, Causes, and Solutions of Hydraulic Presses
The hydraulic press machine is a kind of mechanical equipment. It sometimes has some failures during use. The common hydraulic press failures mainly include:
Serial Number | Common Faults | Causes | Solution |
1 | Movement failure | 1. The electrical wiring is not firm or wrongly connected 2. Insufficient fuel tank pressure control 3. Insufficient oil filling in the fuel tank | 1. Check electrical 2. Properly increase the control oil pressure 3. Fill the oil |
2 | Slider crawl | 1. Air or impurities accumulated in the system 2. Improper adjustment of precision or lack of oil in the column | 1. Check whether the oil suction pipe has entered air or impurities, and then move up and down several times and pressurize. 2. Add engine oil to the column and readjust the accuracy. |
3 | The slider is under pressure when it goes down slowly | Too much support | Adjust the back pressure valve so that there is no pressure in the upper chamber of the upper cylinder. The maximum is not greater than 1MPa. |
4 | The slider slides down seriously after parking | 1. Leakage of cylinder port sealing ring 2. The adjustment pressure of the pressure valve is too small or the valve port is not tight. | 1. Observe the cylinder mouth. If oil leakage is found, it should be replaced. 2. Adjust the pressure check valve port. |
5 | Pressure gauge pointer swings violently | 1. There is air in the oil circuit of the pressure gauge 2. Pipeline mechanical vibration 3. The pressure gauge is damaged | 1. When pressing up, slightly loosen the pipe joint and deflate it. 2. Fasten the pipeline 3. Replace the pressure gauge |
6 | The stroke speed of high pressure is not enough, and the upward pressure is slow | 1. The flow rate of the high-pressure pump is adjusted too small. 2. The pump is worn or burned. 3. The internal leakage of the system is serious. | 1. Adjust according to the instruction manual of the pump. At 25MPa, the pump eccentricity can be adjusted to 5 grids. 2. If the leakage of the oil return port of the pump is large, it should be removed for inspection. 3. First check whether the filling valve is closed, and then check whether the seals of each component are damaged. |
7 | Pressure drops too fast during pressure hold | 1. Oil leaks from various valve ports or pipelines involved in pressure maintenance. 2. The sealing ring in the cylinder is damaged. | 1. Check the sealing conditions of the filling valve and the pressure maintaining and releasing valve. 2. Replace the sealing ring |
Maintenance Method of Hydraulic Press
Today, hydraulic presses are used in a wide range of applications. When the hydraulic press machine encounters some minor faults, they can be resolved by users. There are three main methods of hydraulic press maintenance.
1. Replacement method
Exchange the same components on the hydraulic press of the same type, structure, and principle, and install them in the same position, so that it can quickly confirm whether the replaced components are faulty.
The advantage of this method is that even if the technical level of the maintenance personnel is low, they can quickly apply this method to make correct judgments and treatment of hydraulic machine failures. However, the use of this method must be based on the same type, same structure, same hydraulic principle, and same hydraulic components, so this method has great limitations and certain blindness.
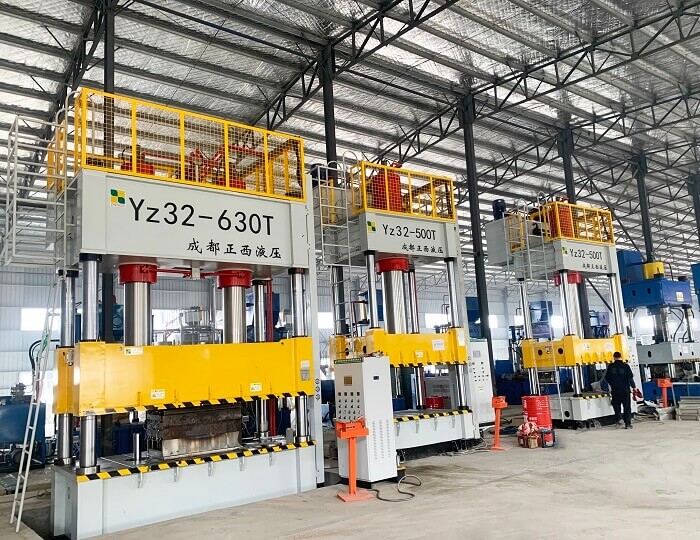
2. Auxiliary method
With the help of simple auxiliary parts, it is possible to diagnose whether the hydraulic components are faulty.
Block the oil port. If the oil port of the hydraulic valve element and the oil port of the cylinder is blocked, it is possible to diagnose whether these hydraulic elements are leaking.
Artificial commutation method. Use the ejector rod to reverse the hydraulic valve element, and it can be diagnosed whether the reversing valve has faults such as stuck, valve core not in place, and so on.
This method allows hydraulic component failures to be diagnosed without dismantling components. Excessive disassembly workload is avoided, the fault diagnosis time is reduced, and quick diagnosis is facilitated. Especially it has very good practicability for failures such as larger oil cylinder seals.
3. Empirical method
Maintenance personnel understands the structure and working principle of each hydraulic component by mastering the hydraulic system theory of hydraulic presses, and on the basis of rich practical experience, conduct a comprehensive analysis of hydraulic press failures and make correct diagnoses quickly.
To sum up, the general failure parts and causes of hydraulic presses can be roughly divided into the following four aspects:
- Improper adjustment of hydraulic components, such as hydraulic pumps, oil motors, sequence valves, directional valves, overflow valves, unloading valves, and balance valve pressure and flow adjustment errors.
- The sealing element is damaged or impurities make the hydraulic element not work normally.
- Hydraulic components are worn or damaged, such as sealing failure of valve components, spring failure, excessive or small clearance, etc.
- The electrical control mechanism of the hydraulic press fails, such as relay failure, bad or damaged button, incorrect installation of the electromagnet, etc.
Zhengxi is a manufacturer focusing on the R & D and production of large and medium-sized hydraulic press machines. We have an IS09001 quality management system and EU CE certification, providing you with a one-stop solution for hydraulic presses.
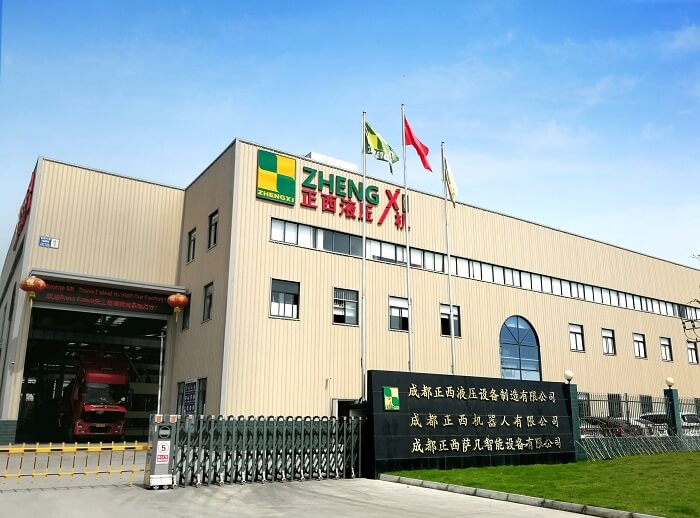