Die forging hydraulic presses are widely used in the automotive industry. They are mainly used for precision forging of key components such as engines and transmission systems. Through processes such as hot die forging and multi-directional die forging, material utilization, production efficiency and product quality are improved, while production costs are reduced. The specific application scenarios and advantages are as follows:
1. Core application scenarios
1) Engine parts
Piston rods and connecting rods: The die forging hydraulic press uses the hot die forging process to press the heated metal billets into shape in a mold at one time, reducing the amount of subsequent machining and improving the fatigue resistance and reliability of parts.
Crankshafts: Large die forging hydraulic presses can forge heavy-duty automobile crankshafts, replacing traditional casting processes, improving material density and mechanical properties, and meeting the requirements of high-load working conditions.
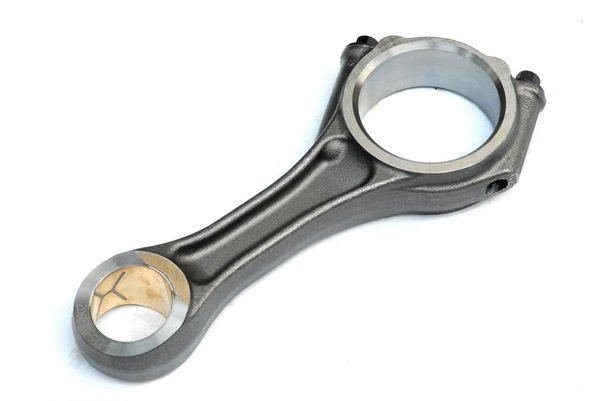
2) Transmission system parts
Gears, half shafts, and drive shafts: The die forging hydraulic press uses high-precision mold design to achieve precision forming of complex structures such as gear tooth profiles and half shaft splines to ensure transmission efficiency and service life.
Flanges: The closed die forging process can forge high-strength flanges to meet the connection requirements of automobile chassis and suspension systems.
3) Lightweight application
Aluminum alloy wheel: Through the warm forging process, the die forging hydraulic press can produce high-strength and lightweight aluminum alloy wheels, reducing automobile energy consumption by more than 40%.
Extrusion forging: Applicable to ordinary round steel forging and aluminum alloy extrusion forging, further expanding the application range of lightweight materials.
2. Technical advantages
1) High precision and high strength
The die forging hydraulic press achieves high-precision control of pressure and position (accuracy of ±1%) through the servo control system, ensuring the consistency of forging size and stability of mechanical properties.
Dynamic recrystallization technology makes the forging structure uniform, improves material utilization by more than 30%, and reduces subsequent processing allowance.
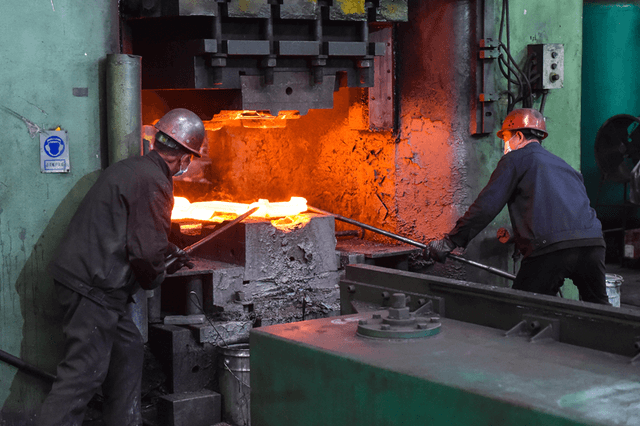
2) Efficient production and automation
The continuity and stability of hydraulic transmission support efficient production. With rapid die replacement and automated production lines, rapid die change and unmanned operation can be achieved.
The upper cylinder design is used for the up and down movement of the slider, and the control console contains a hydraulic pad to achieve the pressure power required for the workpiece stretching and the ejection force required for ejecting the workpiece, further improving production efficiency.
3) Material utilization and cost optimization
The multi-directional die forging process can forge forgings with complex shapes and inner cavities (such as fork shafts). The material utilization rate is 20%-50% higher than that of free forging, significantly reducing the amount of subsequent processing.
The efficient production process and low scrap rate effectively reduce production costs and enhance corporate competitiveness.
4) Safety and reliability
The hydraulic system is equipped with automatic protection devices such as multi-level overload protection, oil temperature alarm, and oil level alarm to ensure the safety of equipment and operators.
The electrical system adopts mature PLC control with complete fault diagnosis functions to ensure production continuity.
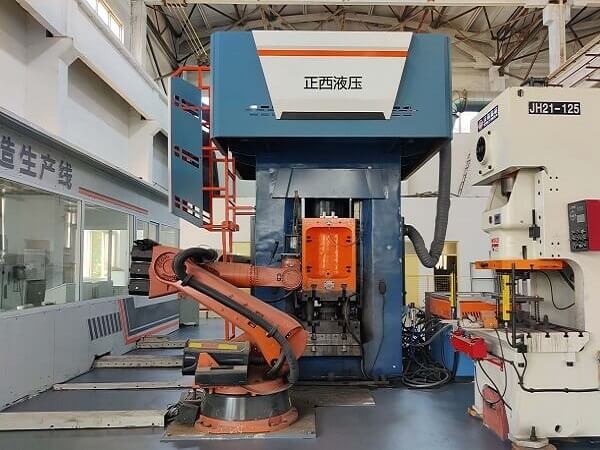
3. Typical cases
1) Fork shaft forging
The multi-directional die forging hydraulic press realizes the one-fire and one-time forming of the fork shaft through the synchronous movement of the vertical extrusion punch, the horizontal die and the extrusion punch. The product has no flash, light weight, high material utilization rate, and the forming accuracy meets the stringent requirements of the automobile transmission system.
2) Aluminum alloy wheel hub production
The fast servo hot die forging hydraulic press adopts a closed frame body and high-precision mold design to achieve warm forging of aluminum alloy wheels. The product size accuracy, and consistency meet the strict requirements of the automotive industry for component accuracy.
3) Heavy crankshaft forging
The 125MN hot die forging press production line manufactured by Erzhong provides large-scale and efficient crankshaft forging solutions for the automotive and railway industries, reducing the cost of forging blanks and improving forging performance.
Zhengxi Intelligent provides high-quality die forging hydraulic presses. If you need it, you can contact us.