Die forging and free forging are two common forging processes in the field of metal processing. They have their own characteristics and applicable scenarios in the processing of metal materials. This article will introduce these two processes in detail in terms of definition, process flow, advantages and disadvantages, etc.
Die forging is a forging process that uses dies or tooling to constrain and guide metal materials into predetermined shapes. In the die-forging process, the metal blank is placed in a special mold, and then pressure is applied to make it subject to extrusion and plastic deformation, gradually forming the desired forging shape. Die forging is often used to produce more complex and precise forgings, such as automotive engine crankshafts, aerospace parts, etc. Since die forging has high requirements for material flow and shape control during the forming process, forgings with high precision and dimensional consistency can be obtained.
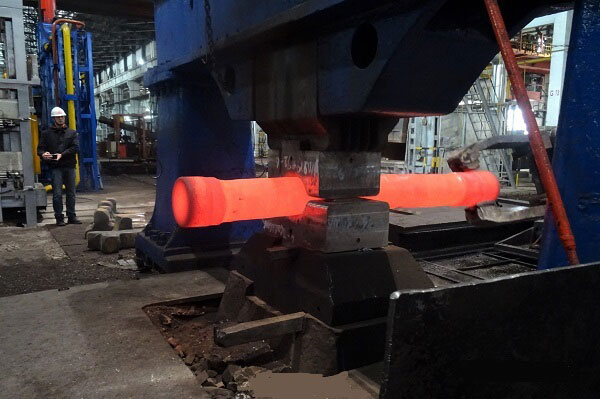
In contrast, free forging is a forging process that does not use dies or tooling. In the free forging process, the metal blank is subjected to the forging force, and it flows freely and changes shape under the force. Free forging is suitable for producing forgings with simple shapes, such as forging hammers, wrenches and other hand tools. Since there is no mold restriction, the production cost of free forging is lower, but the accuracy and dimensional consistency of forgings are usually worse than die forging.
From the process point of view, there are obvious differences between die forging and free forging. Die forging usually requires the design and manufacture of molds, which increases the cost and process preparation time in the early stage of production. But once the mold is manufactured, the production efficiency of die forging is high, especially suitable for mass production of forgings with complex shapes. On the other hand, free forging does not require special molds, and the preparation time is relatively short, which is suitable for small-batch production and urgent processing needs.
Die forging and free forging are also different in terms of production costs and applicable scenarios. Since die forging requires high mold manufacturing costs, it is suitable for large-scale production and the long service life of molds. For example, the automotive industry usually uses die forging to produce engine crankshafts to meet high-volume requirements. Free forging is more suitable for small-scale production or occasions that require flexible shape adjustment. For the production of some small forgings, free forging has certain advantages, because the process parameters can be quickly adjusted according to needs and the production cycle can be reduced.
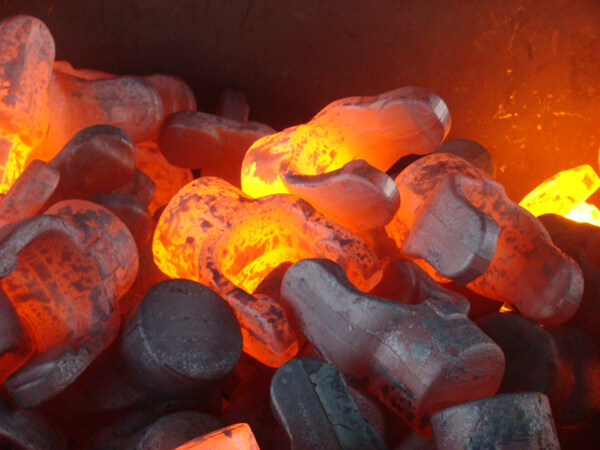
In terms of process flexibility, free forging is significantly better than die forging. Since there is no limitation of the mold, free forging can adjust and change the shape of the forging more flexibly during the forming process. This is of great significance for some special needs or experimental production. However, after the die forging is completed, if the shape needs to be adjusted, a new mold needs to be redesigned and manufactured, which increases the production cost and cycle time.
To sum up, die forging and free forging are two important metal forging processes, each of which has advantages in terms of forging shape complexity, production batch, cost budget, and process flexibility. Choosing the right process depends on the specific production needs and technical requirements. In practical applications, enterprises can reasonably choose die forging or free forging according to the characteristics of forgings and production scale, so as to meet customer needs to the greatest extent and achieve efficient and stable metal forging production.
Zhengxi is a professional forging press manufacturer in China, providing high-quality free forging machines and die forging machines. Customers can choose a free forging machine or a die forging machine according to their needs.