This article mainly introduces the operation of the hydraulic press, including the inspection work before the operation, the operation process, and the maintenance after the operation. Here, you can learn everything related to the operation of hydraulic presses. Hurry up and start reading.
Operating Requirements
- Hydraulic machine operators must be trained to master equipment performance and operating techniques before they can work independently.
- All the operation and use of hydraulic presses should be implemented in strict accordance with the requirements of the operating instructions.
Check Before Starting
- Check the “shift record” to see if there are any abnormalities, so as to avoid hydraulic machines working with problems.
- Apply lubricating oil to the surface of the four columns as required. Check the oil level position, it must not be lower than the minimum liquid level line.
- Check whether the fasteners of the four-column hydraulic press are firm and whether the limit device and safety protection device are complete and reliable. The fasteners include mold buckle grips, limit switches, light curtain sensors, and other fixing and positioning bolts and screws.
- Confirm that the mold is correct. If it is necessary to replace the mold, it must be carried out in a shutdown state. Avoid touching the start switch. Install the upper and lower molds and adjust the mold clearance. It is not allowed to deviate from the center on one side and ensure that the centerline of the slider coincides with the centerline of the mold. The mold should meet the technical requirements and be fastened firmly. Mold fastening requires four-corner fastening, tight both ends or triangular fastening, that is, 4X crimping claws should be pressed against the mold.
- Fill in the inspection record form.
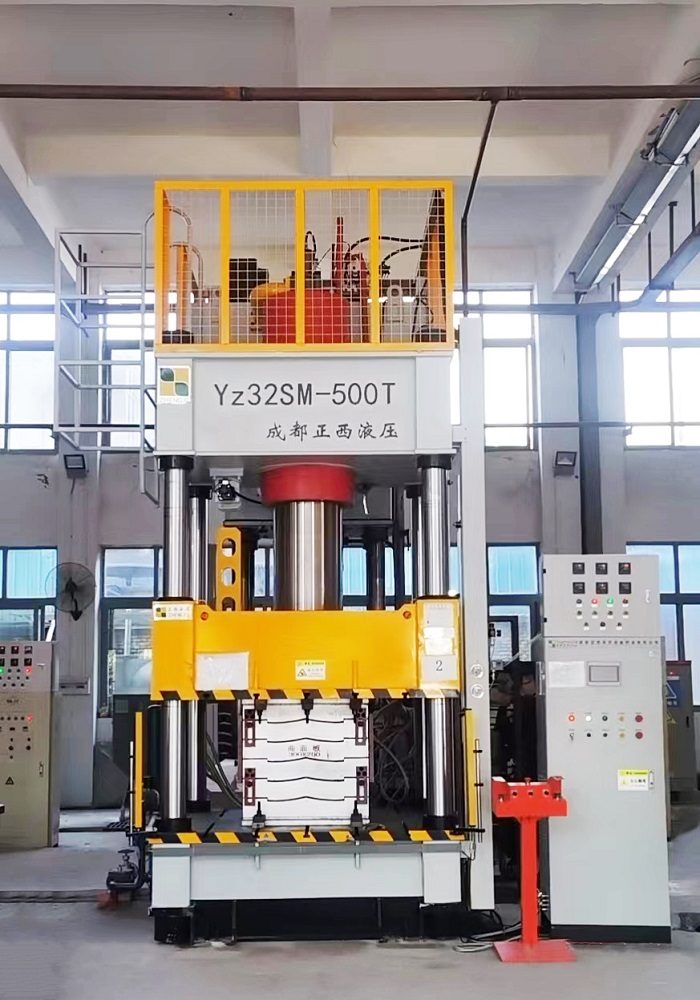
Power-on Inspection Before Work
- Boot sequence:
Turn on the power (side of the console).
The power indicator light is on → Turn and release the emergency stop button → Adjust the position of each selection switch and travel switch according to the process requirements → Adjust the PLC required value according to the process card requirements → Press the start button of motor 1 → Press the start button of motor 2, At this time, the hydraulic pump is in an empty load cycle state. The distribution of the buttons is shown in Figure. - Action sequence:
Fast down→Slow down→Work→Deflate→Stop and hold pressure→Slow back→Fast back→Slow top→Fast top, core pull→Core pull back. - Working status
Manual: The “working state selection” switch is placed in the adjustment state. Each action needs to be done manually.
Semi-automatic: The “working state selection” switch is placed in a semi-automatic state. All actions need to be completed manually. - Rotate to adjust the working state.
Press the “Two Hands Run” button with both hands simultaneously. The slider moves down quickly, and when the set limit is reached, the slider moves down slowly. The upper and lower abrasive tools are closed and pressure maintained until the set time is reached. After the action is completed, the slider slowly returns to the set limit and then returns quickly. At this moment, the slider is in a state of static pressure relief. Repeat for more than 3 times in a row to confirm that the hydraulic press machine can work normally. - When idling, confirm whether the sound of the oil pump is normal. Whether there is any leakage in the hydraulic unit, pipes, joints, and pistons. Whether the pressure gauge is normal. Immediately notify the mechanic and electrician when a problem arises that cannot be resolved. After confirming that the pressure is normal and the working beam moves flexibly, it can work.
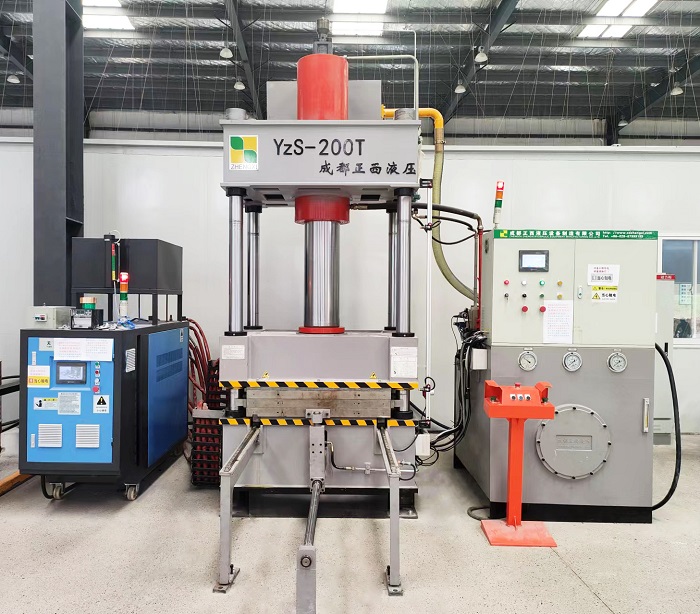
Work
- Before the operation, all kinds of sundries on the mold should be cleaned. The primary mold should be checked for crack damage. Wipe off any dirt on the hydraulic rod. Confirm whether the weight of the material meets the requirements and whether the weighing tool is accurate.
- Turn on the mold heating switch. It can only work after the temperature displayed on the meter rises to the process value.
- Manually press a piece of the workpiece. And then produce after passing the inspection.
- The “working state selection” switch is placed in the semi-automatic state, and the exhaust gas is selected. At this time, the equipment is in semi-automatic mode, and the production process generally uses semi-automatic mode.
- Add the raw materials evenly into the cavity of the fixed model according to the process value.
- Press the “Two Hands Run” button with both hands simultaneously. The slider moves down quickly, and when the set limit is reached, the slider moves down slowly. The upper and lower grinding tools are closed to maintain pressure, and after the set time is reached, the slider returns to release pressure and exhaust. Repeat the same exhaust action three times in a row. After the action is completed, the slider slowly returns to the set limit position, and then quickly returns to its position. At this time, the slider is in a static pressure relief state.
- The jacking cylinder starts to push out the product. The indicator light of the upper limit of the ejection is on, and the pressed product is taken out. The top cylinder is retracted, the lower limit display light is on, and the whole set of actions is completed.
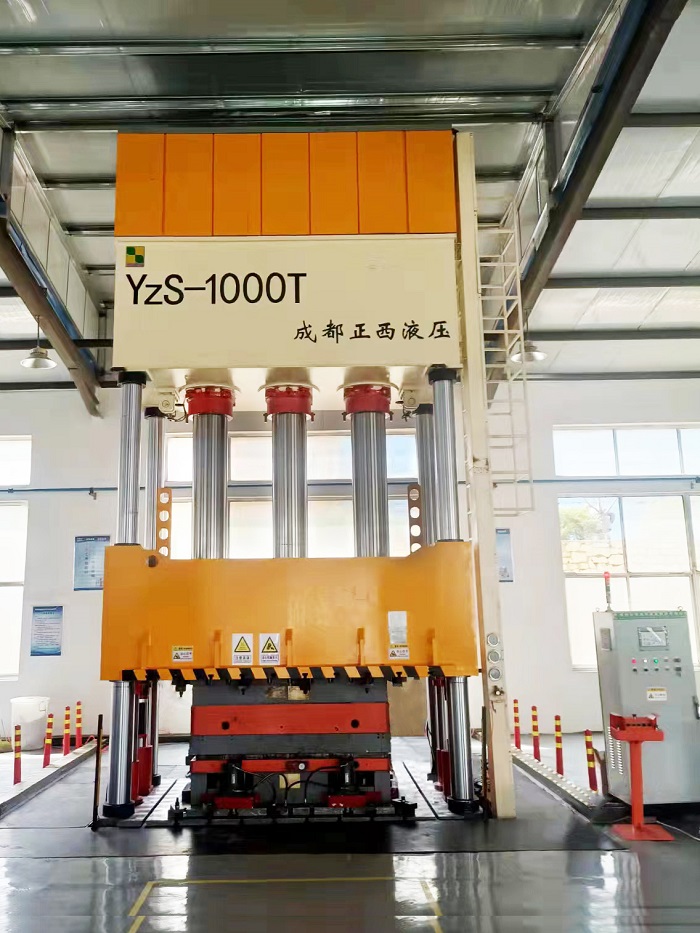
Precautions for Safe Operation
- During the working process of the machine, the mold should not be overhauled and adjusted. The human is prohibited from entering the working area.
- When the machine finds serious oil leakage or other abnormalities (such as unreliable action, loud noise, vibration, etc.), it should stop and analyze the cause. Try to exclude problems. Do not put into production with problems.
- Do not overload or exceed the maximum eccentricity.
- It is strictly forbidden to exceed the maximum stroke of the slider. The minimum mold closing height shall not be less than 280mm.
- It is strictly forbidden to use the machine tool with super performance, the main performance parameters are as follows:
Number | Project | Unit | Specification |
1 | Nominal force | KN | 1000 |
2 | Liquid maximum working pressure | MPa | 25 |
3 | Slider stroke | mm | 600 |
4 | Opening height | mm | 900 |
5 | The maximum stroke of the ejector cylinder piston | mm | 200 |
6 | Preload | KN | 315 |
7 | Mold opening force | KN | 400 |
8 | Master cylinder down speed | mm/s | 120 |
9 | Master cylinder working speed | mm/s | 1-5 |
10 | Master cylinder return speed | mm/s | 100 |
11 | Master cylinder preload speed | mm/s | 8-25 |
12 | Mold opening speed of the master cylinder | mm/s | 4-15 |
13 | Release speed | mm/s | 5-10 |
14 | Effective size of the workbench | mm X mm | 630X630 |
15 | Height of working surface from the ground | mm | 800 |
16 | Working medium | Anti-wear hydraulic oil | 46# |
- The remote pressure adjustment range is 5-25Mpa.
Stop
- Before shutting down, the slider must be lowered and closed with the rigid grinding tool. Return first after starting.
- Press the “emergency stop” button to turn off the oil pump. Turn off the power switch.
- After the hydraulic press is finished, wipe the hydraulic rod of the press clean. Add lubricating oil, clean the mold and workpiece, and place them neatly.
- Clean up the working environment to ensure that the working environment of the hydraulic press is clean.
- Fill in the “Shift Handover Record” and do a good job in the shift handover work.
Maintenance
- It is recommended to use No.46 anti-wear hydraulic oil for working oil. The operating environment temperature is within the range of 15C~40C.
- The oil should be strictly filtered before it is allowed to be added to the oil tank.
- The working oil should be replaced once a year. The time for the first replacement should not exceed three months.
- The slider should be filled with lubricating oil frequently. The exposed surfaces of columns and plungers should always be kept clean. Oil should be injected before each work.
- Under the nominal pressure of 100T, the maximum allowable eccentricity of the concentrated load is 2mm. Excessive eccentricity will easily cause other bad phenomena in the column.
- Calibrate and check the pressure gauge every six months.
- If the machine is not used for a long time, all the processing surfaces should be cleaned and coated with anti-rust oil.
Zhengxi is a professional hydraulic machine manufacturing company with experienced personnel who can provide useful and professional hydraulic machine-related knowledge. Follow us to learn more.